かんたんデジタル現場帳票「tebiki現場分析」を展開する、現場改善ラボ編集部です。
製造業や工場での「タブレット導入」とは、紙の帳票やマニュアル、作業指示書などをデジタル化し、タブレット端末(iPadなど)を通じて現場業務を効率化・高度化する取り組みです。タブレットの導入は「現場DX(デジタルトランスフォーメーション)」の一環として、製造現場の見える化や属人化の解消、さらには人材育成や安全対策の強化にもつながる重要な施策となりつつあります。
この記事では、製造業にタブレット導入が求められている背景から紹介するとともに、導入メリットや実際の成功事例、導入の推進方法を、日々現場DXを実際に支援する立場から解説します。
目次
多くの製造業や工場がタブレット端末を導入し始めている背景
製造現場の効率化・見える化を実現する手段として、iPadなどのタブレット端末の導入が急速に進んでいます。背景には、環境変化とDX(デジタル変革)の必要性があります。ここではそうした背景について以下の3点を重点的に解説していきます。
- 製造業を取り巻く環境変化
- 現場DX(見える化)の重要性の高まり
- 従来の紙帳票の限界
製造業を取り巻く環境変化
近年、製造業はかつてない環境変化が起こっています。代表的なものに「深刻な人手不足」「多品種少量生産への対応」「品質に対する要求水準の高度化」が挙げられます。
厚生労働省の令和6年に発表した「一般職業紹介状況(令和5年12月分及び令和5年分)について」によれば、製造業の有効求人倍率は約1.74倍と、全産業平均の1.27倍を大きく上回っています。 これは、求職者1人に対し約1.74件の求人があることを示し、人材確保が困難な状況を意味しており、つまりは深刻な人手不足があることが言えるでしょう。
また、国立社会保障・人口問題研究所の「年齢(3区分)別人口および増加率の将来推計」によると、2020年に7,509万人だった生産年齢人口は、2060年には5,078万人に減少すると予測されています。生産年齢人口の減少は、製造現場における若年労働力の不足を引き起こし、生産性の低下や技術継承の難しさを招いています。
さらに、消費者のニーズの多様化により、製造業では多品種少量生産が求められており、グローバル化の進展に伴った製品の品質基準が一層厳格化が進行。
※現在、セミナー動画「多品種少量生産における製造品質向上の攻めどころ」を無料公開中
こうした課題を背景に、紙ベースでは限界のある情報管理を見直し、タブレットなどを活用して現場のデジタル化を進める必要性が高まっています。
現場DX(見える化)の重要性の高まり
製造現場におけるDX(デジタルトランスフォーメーション)は、先進企業だけの取り組みではありません。特にDXの中でも「製造業の見える化」は生産工程・設備稼働・品質管理などの分野において、状況をリアルタイムに把握し、判断・改善につなげられる活動です。
従来、作業の進捗やトラブルの兆候は「ベテランの感覚」や「口頭報告」に依存していた部分が多く、属人化と伝達ミスが大きな課題でした。タブレット端末を使って情報をその場で記録・共有すれば、現場全体の動きが数字や記録で明確になります。
例えば、傾向管理という手法と組み合わせることで、データをもとに問題の傾向を掴み、先手を打つ改善活動が可能になる、というような取り組みです。
数字と記録が明確になれば、改善点が見えるため、作業の効率化はもちろん、ヒューマンエラーの抑制や品質トラブルの予防にも直結するでしょう。
ヒューマンエラーの未然防止に課題を感じている方は、資料「製造業におけるヒューマンエラーの未然防止と具体的な対策方法(pdf)」も参考にしてみてください。人的ミスが起きない具体的な仕組み作りについて解説されています。
「紙帳票」の限界
製造業の現場では、長年にわたり紙の帳票が使われてきました。しかし、デジタル化が進む現代において、紙帳票による情報管理に限界が生じています。
▼課題が多い紙帳票の例▼
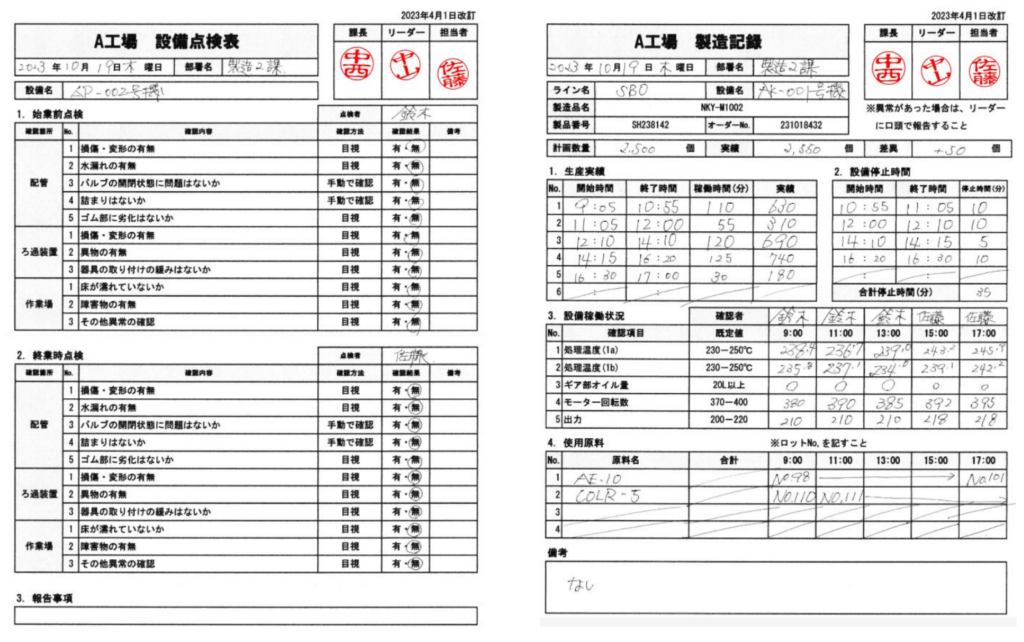
まず、記録された情報はリアルタイムに共有されず、管理者が各所を巡回して確認する必要があるため、反応が遅れがちです。さらに、手書きによる記入ミスや読みづらさ、用紙の紛失・破損といったリスクも無視できません。また、記録がバラバラに保管されていることで、後から必要な情報を探し出すのにも大きな手間と時間がかかります。
品質トラブルや監査の場面では、紙帳票の検索性の低さや保管スペースの問題が浮き彫りになります。特にトレーサビリティが求められる食品・精密機械分野では、紙運用のままでは対応に限界があるのです。
これらの問題を解決する手段が「現場帳票のデジタル化」です。帳票データが電子化されることで、現場に設置されたタブレット端末から記録・確認・共有を即座に行えるようになり、紙ベースでは実現できなかったスピード・精度・柔軟性を手に入れることができます。
例えば以下の画像は、デジタル現場帳票サービス「tebiki現場分析」で可視化された帳票データのダッシュボードです。
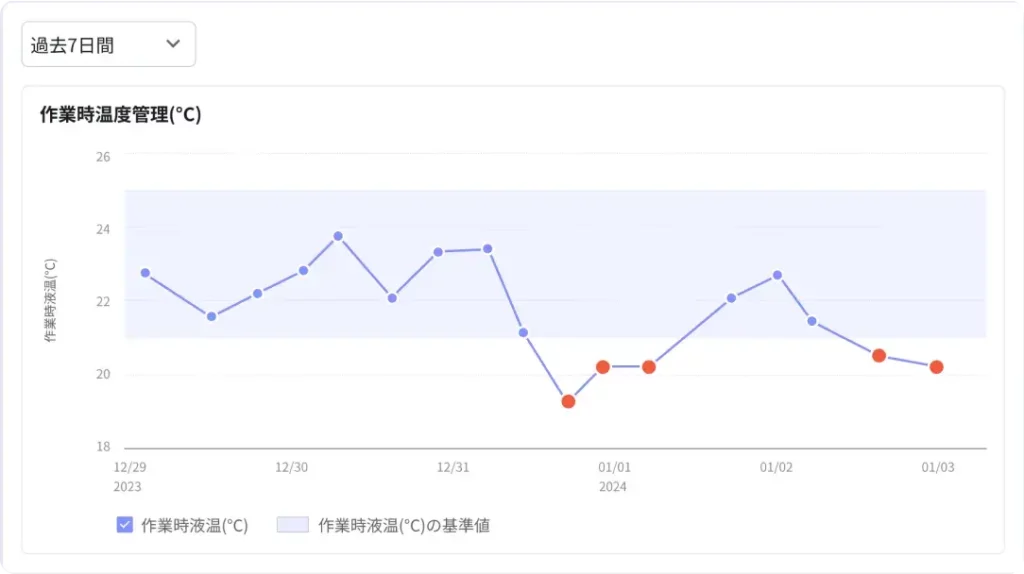
紙の現場帳票よりも分かりやすく、リアルタイムのデータ記録も可能なので、問題や不良の予測や未然防止が可能になります。デジタル現場帳票の詳細なメリットや活用例について理解を深めたい方は、以下の資料「はじめての現場帳票デジタル化ガイド(pdf)」をご覧ください。
製造業・工場にタブレット端末を設置するメリット
製造業や工場において、タブレット端末の導入は単なる機器更新にとどまらず、現場全体の生産性・品質・安全性を高めるための投資と言えます。その具体的なメリットを以下の7つの視点で紹介します。
- 業務効率化や生産性向上
- データに基づいた正確な意思決定が可能に
- ペーパーレスによるコストや管理工数の削減
- リアルタイム異常発見と即対応
- ヒューマンエラーや労働災害の未然防止
- 技術継承や多能工化といった新人教育の促進
- 従業員のスキルセットを可視化
業務効率化や生産性向上
タブレット端末の最大の利点は、業務のスピードと正確さを劇的に向上させる点にあります。作業指示、検査結果、点検記録などを紙でやり取りしていた場合、記入・回収・確認・保管まで多くの手間が発生します。しかしタブレットを使えば、すべての工程を「その場」で完結させることが可能です。
また、変更された仕様や注意点をリアルタイムで共有できるため、作業ミスや指示の遅延も防止できます。結果として、管理者が都度現場を巡回する必要がなくなり、少人数でも効率的な現場運営が実現します。さらに、チェックリストや日報の自動化により記録精度が上がり、再確認の工数も削減可能です。
無駄な待ち時間や移動時間が減り、製造工程にかける集中力と時間が確保され、生産性の底上げにつながるでしょう。
製造業や工場における生産性向上は、タブレット導入以外にも数多くの打ち手が存在します。詳細は以下の記事でご覧いただけるので、生産性の改善手法や事例について知りたい方はあわせて参考にしてみてください。
関連記事:製造現場の生産性が67%向上した事例や改善方法【指標や計算式も解説】
データに基づいた正確な意思決定が可能に
タブレットでの運用により、日々の作業・点検・品質チェックのデータを自動的に蓄積・分析できるようになります。
蓄積されたデータは、異常の傾向、作業者ごとの実績、設備の稼働状態など、多角的な視点で可視化され、管理者は感覚ではなく「数値」を根拠に判断できるようになります。数値によって判断することで、工程改善や投資判断、品質管理の精度が格段に高まります。
従来、製造現場の判断はベテラン社員の経験や勘に依存する現場(=属人化)が少なくありませんでした。しかしデータ活用を通じた意思決定が可能な体制が整備できれば、属人化からの脱却が図れるのです。
とはいえ、「データ活用を通じた現場改善」と言われても、具体的にどのような改善手法を実施することになるのか、いまいちピンと来ない方もいると思います。そこで、ただいま無料公開中のセミナー動画「カイゼンにつなげる製造現場のデータ活用」では、製造現場におけるデータ活用の進め方やポイントについて解説されているので、参考にしてみてください。データ活用の具体的なイメージがつくようになるはずです。
下の画像をクリックすると、視聴申し込みページに遷移します。隙間時間にご覧いただけるので、お気軽にお申込みください。
ペーパーレスによるコストや管理工数の削減
製造現場では、現場帳票や紙マニュアルなど、紙の資料が膨大に使われてきました。特に多品種少量生産が進む現代では、作業ごとに帳票やマニュアルが増え、印刷・配布・保管・更新の手間が大きな負担となっています。
タブレット端末の導入により、紙媒体をすべてデジタル化すれば、印刷コストはもちろん、資料を探す・運ぶ・保管する手間が一気に削減されます。作業手順書も動画や画像でわかりやすく表示できるため、情報の伝達ミスも防げます。
また、マニュアルの改訂もシステム上で一括反映できるため、古い情報を誤って参照するリスクを軽減できます。製造業におけるペーパーレス化は環境配慮という側面だけでなく、日々の運用コストや管理工数の削減という極めて実務的なメリットもあると言えます。
ペーパーレスの具体的な進め方はいくつかありますが、それらがまとめられた資料「製造現場の生産性を向上するペーパーレスの進め方(pdf)」を参考にすると、ペーパーレスの実践ヒントが得られるでしょう。あわせて参考にしてみてください。
リアルタイム異常発見と即対応
タブレットを活用すれば、製造工程中に発生する異常やトラブルをリアルタイムで検知し、即座に対応することが可能になります。例えば、点検記録やセンサー連携により基準値から逸脱した項目が自動的に通知され、作業者や管理者にアラートを出す仕組みが作れれば、異常をすぐに検知できます。
もちろんこれは、アラート機能が備わったデジタル現場帳票でなければ実現できないですが、アラート機能がなくとも「データをリアルタイムで計測・閲覧できる環境」が最低限構築されれば、未然防止に寄与する現場が整備できます。
さらに、異常内容はその場で写真や動画付きで記録・共有できるため、トラブルの原因究明や再発防止策の立案もスムーズになります。
紙帳票の確認漏れや報告の遅れによって、手遅れになるケースも少なくないでしょう。そこで、リアルタイムでの可視化と即応体制の構築によって、現場は「事後対応型」から「予防型」の運営へとシフトできます。
関連記事:異常検知とは?機械学習不要で実施できるツールも紹介!
ヒューマンエラーや労働災害の未然防止
ヒューマンエラーや労働災害は、製造業にとって大きなリスクです。作業手順の確認不足や伝達ミス、記録の書き間違いが事故や不良品の原因になることもあります。
タブレットを活用すれば、作業手順を動画やイラスト付きで分かりやすく表示できるので、正しい作業手順の浸透が図れるとともに、従業員の安全作業に寄与すると言えます。また、伝達や記録系の作業は手書きに比べてミスが減りやすく、工場全体の品質向上にもつながります。
とはいえ、タブレット導入だけでヒューマンエラーをすべて撲滅できるわけではありません。人的ミスを完全に再発防止するには、本質的な原因を突き止め、適切な対応を取る必要があります。ただいま無料公開中のセミナー動画「繰り返す品質・安全トラブルを防ぐには?効果のある再発防止策と現場で活かせる具体例」では、ヒューマンエラーの再発防止策が体系的に解説されているので、あわせて参考にしてみてください。
下の画像をクリックすると、視聴申し込みページに遷移します。隙間時間にご覧いただけるので、お気軽にお申込みください。
技術継承や多能工化といった新人教育の促進
技術継承が難しくなっている今日、タブレットは若手・外国人・未経験者への教育ツールとしても有効です。紙のマニュアルでは伝えきれなかった手順や細かいコツも、動画や写真で直感的に学べるため、理解度や定着率が格段に高まります。
また、ベテラン作業者の技術やノウハウを動画として記録・共有することで、「暗黙知」を「形式知」へと変換し、属人化を防ぐことが可能です。さらに、タブレットを用いて複数の業務マニュアルや作業履歴を一元管理することで、多能工化の促進にもつながります。
具体的な技術継承の進め方については、資料「技術伝承を成功させるポイント(pdf)」で詳しく解説されているので、あわせて参考にしてみてください。
>>>資料「技術伝承を成功させるポイント(pdf)」を読んでみる
従業員のスキルセットを可視化
タブレット端末は、従業員のスキルや作業実績を見える化するプラットフォームとしても有効です。例えば、作業者ごとの対応可能な工程や、習得済みのマニュアルといった「スキルマップ」がタブレット上で見れれば、最適な人員配置や育成計画の立案・多能工化の推進が可能になるでしょう。
▼スキルマップのイメージ例▼
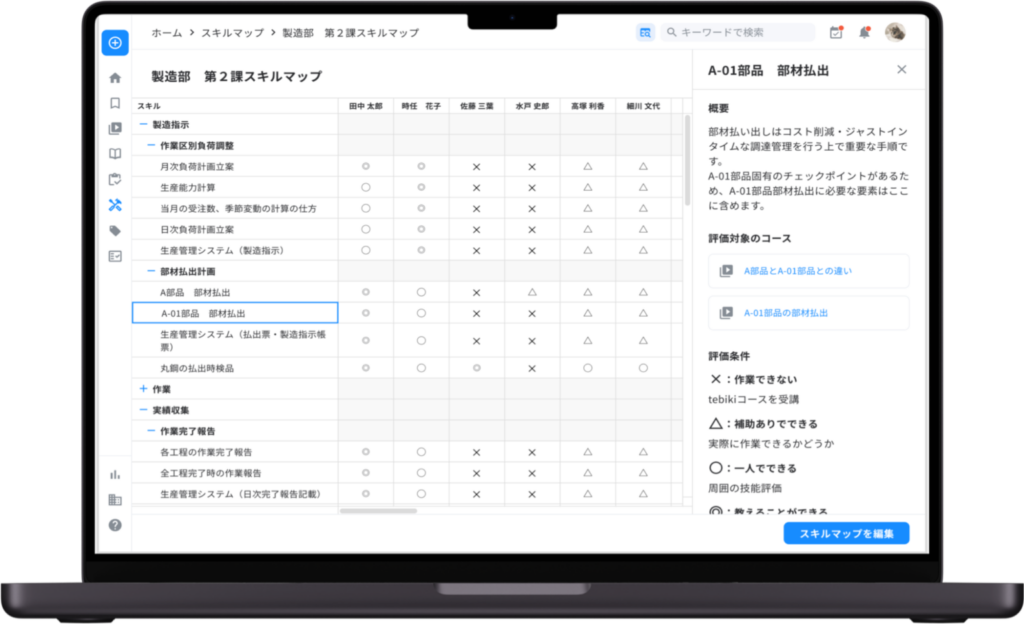
【「クラウド型スキルマップ – tebiki現場教育」より抜粋】
また、客観的なスキルにもとづいた人事評価や資格更新の判断にも活用できるため、評価の透明性と納得感も向上するでしょう。
特に製造業は多国籍人材が混在する現場が多いので、作業者ごとの理解度や業務適性の可視化(スキル管理)は重要です。タブレットを導入することによって「誰が何をできるか」を明確にし、組織全体の生産性を高めるべきでしょう。
スキル管理をするための環境整備は難しく、たとえ整備できても形骸化するケースも珍しくありません。しかしながら、生産性が向上している工場の多くはスキル管理のための環境整備に成功しています。資料「現場力を高めるスキル管理のコツ(pdf)」では、計画的な人材育成を可能にするスキル管理のコツや進め方が解説されています。あわせて参考にしてみてください。
タブレットやスマホ導入で工場を改善した製造業事例
タブレットやiPad、スマホの導入によって工場を改善した製造業事例として、ここでは以下の5つの事例を紹介します。
- 作業日報と前処理管理表をデジタル化
- リアルタイムデータによる品質不良の早期発見と未然防止
- 暗黙知を可視化し、OJT教育工数を大幅削減
- マニュアルの作成工数を7割削減
- 外国人労働者の即戦力化・作業品質の向上
作業日報と前処理管理表をデジタル化
共栄工業株式会社は、1948年創業のスチール製家具メーカーで、近年では納骨壇や宅配ボックスといった社会課題の解決を目的とした製品開発にも取り組んでいます。品質と環境への配慮からISO9001・ISO14001も取得し、製造現場の記録・管理体制を強化してきました。
しかし現場では、以下のような課題に悩まされていました。
- 作業日報や前処理管理表などの帳票を紙に記録し、それを毎日Excelに転記・集計
- 1日2時間以上の非効率な作業が常態化
- 記録が目的化し、肝心の改善活動が後手に回る
そこで現場帳票をデジタル化し、スマホから現場のデータを記録・共有できる体制を整備。導入後は、記録と集計が一体化され、集計作業はわずか1分に短縮。入力と同時にダッシュボードへ反映されるため、朝礼時点で分析・改善アクションを取れる体制が整いました。
▼ダッシュボードで分析する様子▼
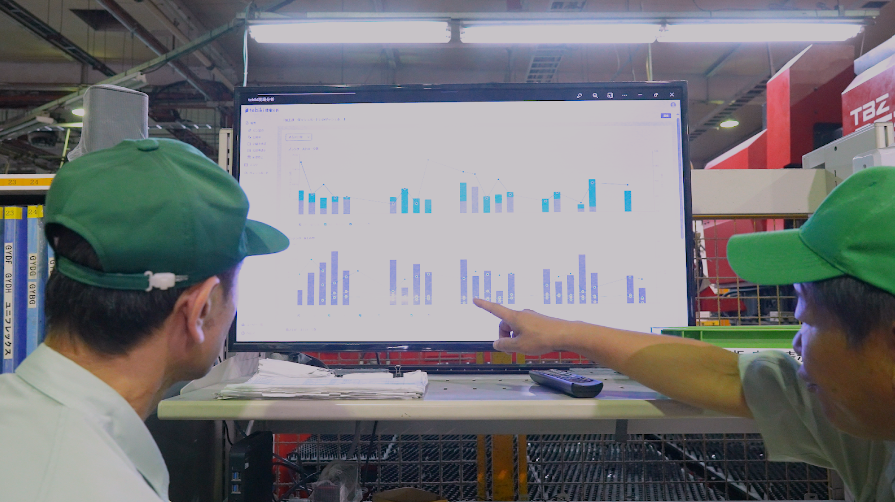
作業状況もリアルタイムに見える化され、意思決定のスピードと精度が飛躍的に向上しています。同社の詳しい事例は以下のインタビュー記事から参照できるので、あわせてご覧ください。
インタビュー記事:1日2時間の集計作業が約1分に。スチール製家具製造の共栄工業のデジタル改革
リアルタイムデータによる品質不良の早期発見と未然防止
株式会社日本電気化学工業所は、1935年創業の老舗メーカーで、アルミニウムの表面処理、特にアルマイト加工に特化した企業です。建材、自動車、航空機、電子機器といった幅広い業界に向けて高品質な処理技術を提供しています。
同社が抱えていた課題は以下のとおりです。
- 異常値の発見に時間がかかっていた
- ゆえに迅速な対応ができなかった
- 収集したデータが改善活動にうまく活用されていなかった
- 現場を巡回して紙帳票に押印・承認する作業が膨大だった
こうした非効率な業務フローは、品質トラブルのリスクや現場負担を高める要因となっていたのです。
同社はこうした課題を解決するために、タブレットを導入し、現場データをリアルタイムで監視・蓄積・分析できる体制を整備しました。現在は、微細な異常の早期発見や迅速な対応ができています。
▼タブレットで記録・集計したデータを分析する様子▼
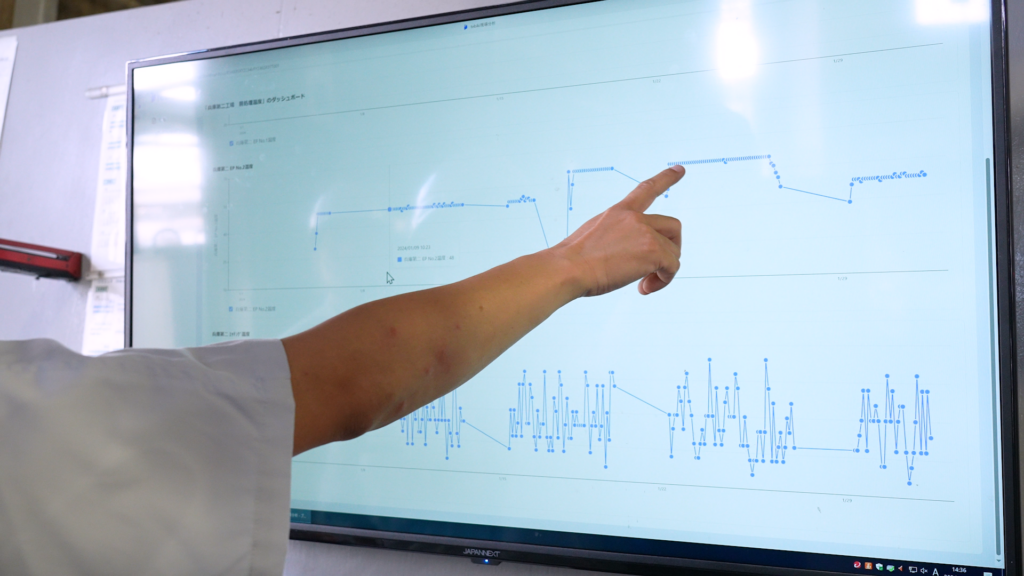
例えば、温度変化から設備異常を事前に察知し、ライン停止を未然に防ぐなど、現場での判断精度が格段に向上。また、異常値の自動通知や、全記録の一括承認機能により、管理者の業務負担も大幅に軽減されました。結果として、品質の安定化と現場の意識改革を同時に実現しています。
同社の詳しい事例は以下のインタビュー記事でご覧いただけます。
インタビュー記事:品質不良の未然防止をリアルタイムデータで実現。異常値検知を迅速にできた理由。
暗黙知を可視化し、OJT教育工数を大幅削減
アサヒ飲料株式会社は、アサヒグループに属する大手飲料メーカーで、「三ツ矢」「ウィルキンソン」「カルピス」「アサヒおいしい水」などの人気ブランドを多数展開しています。
同社の富士吉田工場では、人材育成について以下のような課題がありました。
- OJT教育の担当者ごとに教え方がばらついていた
- ゆえに新人の理解度にばらつきがあった
- 手順書の作成に膨大な工数がかかっていた
- 手順書の改訂作業にも多大な時間と負荷がかかっていた
こうした課題を解決するために同社は、タブレットを導入し、動画マニュアルを整備しました。
▼タブレットで動画マニュアルを撮影する様子▼

作業のコツや背景まで含めて視覚的に伝えられるようになり、教育内容の標準化と工数削減を同時に実現。手順書作成の所要時間は3分の1に、OJTの負担も半日から最大2時間にまで短縮されました。また、動画で形式知化されたマニュアルにより、熟練者の“暗黙知”の継承も可能となり、スキルの早期定着も実現しています。
同社の詳しい事例は以下のインタビュー記事から参照できるので、あわせてご覧ください。
インタビュー記事:OJTや手順書作成工数を大幅に削減!熟練者の暗黙知も動画で形式知化
マニュアルの作成工数を7割削減
児玉化学工業株式会社は、1946年創業の化学メーカーで、自動車部品・住宅設備・エンターテイメント製品の製造を手がける企業です。
現場には日本人だけでなく、スペイン語・ポルトガル語・ベトナム語・中国語など多様な言語を話す外国人従業員も多数在籍しています。そんな同社が抱えていた最大の課題は、「伝わらない教育」です。膨大な紙の手順書は分かりづらく、外国人には日本語の壁がありました。
加えて作業のコツや動きといった暗黙知が文字や写真では伝えきれないという限界もあり、「教える人によって言っていることが違う」「夜勤と日勤で伝わり方が異なる」といった声も多く、不良品の発生や手順ミスにつながっていました。
こうした課題を一掃するために、同社はスマホによる動画マニュアルの導入を決断。結果、紙の手順書の作成工数は3分の1にまで削減され、教育の標準化が進みました。撮影・編集がスマホで簡単にでき、音声入力や翻訳機能で多言語化にも対応。動画を通じて、作業のなぜそうするのかまで可視化され、熟練者のノウハウを新人が素早く習得できるようになりました。
同社のインタビュー動画を以下に掲載しているので、参考にしてみてください。
▼スマホを活用した動画マニュアルを整備している同社のインタビュー動画▼
詳細な事例を記事で読みたい方は以下のインタビュー記事をご覧ください。
インタビュー記事:手順書作成の工数は紙の1/3になったと思います。動画で作るのはかんたんだし、学ぶ側にもわかりやすいですよね。
外国人労働者の即戦力化・作業品質の向上
日世株式会社は、日本唯一のソフトクリーム総合メーカーです。主力商品であるコーン・ミックス・フリーザーの製造を通じて、高品質・高安全の商品を全国に供給しています。
同社が抱えていた課題は以下の3点でした。
- 外国人労働者への教育の難しさ
- 非効率な新人研修
- 職人技の技術伝承
従来の紙マニュアルや口頭講義では、言語や解釈の壁によって正確な理解が得られず、現場ではトラブルやヒヤリハットが発生する要因となっていました。また、研修担当者が毎週何時間も新人講義に費やすことで負荷がかかり、教育の質にもバラつきが生じていたのです。
そこで同社は、動画マニュアルによる教育体制の整備を決意。作業現場の手順や機械のメンテナンス方法などを動画で記録し、タブレット上で視覚的かつ繰り返し学べる環境を構築しました。
また、同社が導入した動画マニュアル作成ツール「tebiki現場教育」の自動字幕翻訳機能によって、ベトナム・中国・フィリピンといった外国人従業員の教育も効率的に実施できるようになり、外国人従業員の理解度テストでは正答率が100%に到達するなど、大きな成果を上げました。
※動画マニュアル作成ツール「tebiki現場教育」の詳細機能や活用事例がまとめられたサービス資料はこちら
加えて、講義時間は従来の1/10にまで削減され、教育者は業務負担を減らしつつ、より本質的な業務改善や教材開発に注力できるようになっています。
同社の詳しい事例は以下のインタビュー記事から参照できるので、ぜひチェックしてみてください。
インタビュー記事:新人研修の手間が1/10に!自動字幕翻訳で、外国⼈スタッフの理解度テスト正答率が100%になりました。
タブレットで工場を見える化するための施策
タブレットの導入は「手段」であり、それ自体に大きな価値があるわけではありません。工場の見える化を実現するためには、タブレット導入に連動させた「施策」が必要です。以下の2つの仕組みと組み合わせることで、タブレットは初めて生産現場の改善ツールとして機能します。
- 現場帳票のデジタル化
- 動画マニュアルを活用した教育体制の整備
現場帳票のデジタル化
工場でタブレットを導入する場合、タブレットで管理するデータの源泉が必要です。一般的には、紙の帳票を電子化し、帳票データをタブレットで閲覧・管理・共有する現場改善がよく取り入れられています。
記録された情報をリアルタイムに集計・可視化できるようになれば、異常の早期発見や改善のスピードが劇的に向上します。
例えば、紙では発見が遅れていた温度異常や記録ミスも、タブレットでの入力と自動チェック機能で即座に察知可能になります。ただし、帳票のデジタル化には「入力しやすさ」「現場負担の少なさ」が大切なため、既存の紙帳票をただタブレットに置き換えるのではなく、現場での操作性まで設計した運用が求められます。
おすすめのデジタル現場帳票である「tebiki現場分析」のサービス資料は、以下の画像をクリックしてダウンロードできます。どういった機能が実際に備わっているのか確認できるため、参考にしてみてください。
動画マニュアルを活用した教育体制の整備
デジタル現場帳票以外で、タブレットがよく使用される場面としては「動画マニュアルの撮影・閲覧」です。
特に製造業や工場における業務は、高度な専門性が求められることに加え、複雑な業務プロセスを踏まなければならないことが多く、「視覚的な理解が促せる教材」が多くの現場で求められています。
また、外国人労働者の比率が大きい現場では、日本語で作られた手順書では教育が非常に難しく、「非言語マニュアル」が必要になります。
こうした課題に対して動画マニュアルは有効手段の1つと言えます。動画マニュアルによって教育体制を改善している現場は徐々に増えてきているのは、上記のような背景があるからなのです。
製造業向けに設計された動画マニュアル作成ツール「tebiki現場教育」の資料は以下の画像をクリックしてダウンロード可能ですので、ぜひチェックしてみてください。
まとめ:タブレット導入は「現場分析」と「現場教育」に寄与する
製造業の現場では、少子高齢化や多品種少量生産、品質要求の高度化など、従来のやり方では対応しきれない課題が山積しています。
こうした背景から、工場の現場においてタブレット端末を活用したデジタル化が急速に進んでいます。しかし、タブレットを導入するだけでは十分ではありません。
業務効率化や品質向上を実現するには、現場帳票のデジタル化や動画マニュアルによる教育体制の構築といった具体的な施策が不可欠です。実際に、さまざまな企業がタブレットとシステムを組み合わせることで、業務時間の削減、ヒューマンエラーの防止、技術伝承の効率化など、目に見える成果を上げています。タブレット導入はゴールではなく、業務改善のスタートライン。現場の課題に即した運用を設計することで、真の意味での「見える化」と生産性向上を実現できるのです。
タブレット導入とあわせて検討したい施策が「デジタル現場帳票」と「動画マニュアル」の2つであることを本記事では解説しましたが、それぞれ製造業での支援実績が多数あるtebikiに少しでも興味があれば、以下の画像をクリックしてサービス資料をダウンロードしてみてください。