かんたん動画マニュアル作成ツール「tebiki現場教育」を展開する、現場改善ラボ編集部です。
職場での重大な事故や災害の多くは、実は「わかっていてもやってしまう」不安全行動に起因しています。
「これくらい大丈夫」「面倒だから」「慣れているから」といった油断や思い込みが、取り返しのつかない事態を招く場合もあるため、発生を防ぐために十分は対策を講じておく必要があります。
そこでこの記事では、不安全行動の類型や原因、実際の事例をもとに、対策と企業の取り組みまで徹底解説します。
目次
不安全行動とは?概要について
不安全行動とは、労働者が「大丈夫だろう」「面倒くさい」などの判断で安全ルールを無視する行為を指し、重大な労働災害の多くがこの行動に起因しています。ここでは不安全行動について具体的に以下の3点を深掘りして解説します。
不安全行動の類型
不安全行動には、厚生労働省が定める以下の12の類型があります。
- 防護・安全装置を無効にする
- 安全措置の不履行
- 不安全な状態を放置
- 新たな危険を作る
- 機械・装置等の指定外の使用
- 運転中の機械・装置等の掃除、注油、修理、点検等
- 保護具、服装の欠陥
- 危険場所への接近
- その他の不安全な行為
- 運転の失敗(乗物)
- 誤った動作
- その他
上記は全て「あるべき姿」から逸脱した行為であり、ルールや基準を理解していながら行われる点が特徴であり、企業はこれらの類型ごとに具体的な対策を講じる必要があります。
特に多いのが「作業効率を優先する」「慣れからくる過信」によるもの。些細な判断ミスやルール軽視が大きな災害につながるケースも少なくないので、現場では常に「あるべき姿」を意識した作業が求められます。どうすれば不安全行動を排除できるのかを先に知りたい方は『不安全行動をなくすには?発生を防ぐための具体的な対策』で紹介しています。
ヒューマンエラーとの関係性
不安全行動とヒューマンエラーは混同されがちですが、明確な違いがあります。ヒューマンエラーは「意図せず起こるミス」である一方で、不安全行動は「リスクを認識しながら意図的に行う行動」です。
つまり、ヒューマンエラーは見間違いや記憶違いなど無意識の行為、不安全行動は「やってはいけないと知りながら実行する」点に本質的な違いがあります。違いはあるものの、実際の現場では両者が重なって発生するケースも多く、対策を講じるにはどちらの視点からの対策が必要です。
なお、ヒューマンエラーがきっかけとなって発生するのがポカミスです。主に製造業で使われる言葉で、人的なミスが要因になって、品質不良や安全トラブルなどの問題を引き起こす行為のことを指します。不安全行動を起点としてポカミスが発生し、場合によっては大きな災害に発展することもあるので、十分な対策は欠かせません。
ポカミスが発生する原因や防止するための対策方法などを詳しく知りたい方に向けて、専門家による解説動画を用意しています。以下の画像をクリックするとご覧いただけます。
不安全行動をする心理には認知バイアスが関係していることも
不安全行動には認知バイアスが関係していることがあります。ここでは具体的に以下の2点との関係を解説します。
確証バイアス
確証バイアスとは、自分に都合の良い情報ばかりを集め、悪い情報や不利な情報を無視してしまう心理傾向のことです。例えば、作業現場で「このやり方で問題なかった」と思い込んでいると、リスクを指摘されても「大げさだ」と受け流してしまいがちになります。
また、新しい安全対策を導入しようとしても「以前からの方法で問題なかったから」と抵抗感を抱く人もいます。このように確証バイアスは、過去の成功体験や思い込みが強く、合理的な判断を妨げます。対策としては、自分の考えをあえて否定する視点を持つこと、多様な意見に耳を傾けること、そして客観的なデータをもとに判断する姿勢が求められます。
ベテランバイアス
ベテランバイアスとは、経験豊富な労働者が「自分は大丈夫」「これまでも問題なかった」と過信し、新たなリスクを軽視してしまう心理のことです。過去の経験が豊かであること自体は強みですが、それが裏目に出て、安全手順の省略や独自判断による逸脱行動を招くことがあります。
例えば以前の失敗と似た状況が再び起きた際に、「あの時も大丈夫だった」と正確なリスク評価を怠ることが挙げられます。ベテランバイアスの怖い点は、本人に自覚がないままリスクを過小評価してしまうことです。
対策としては、定期的な安全教育とリスク認知のアップデートが効果的です。ベテランこそ常に初心に戻る意識をもち、現場のルールや手順に忠実であることが、事故の防止につながります。
不安全行動と不安全状態の違い
不安全行動と似た言葉に「不安全状態」があります。不安全状態とは、機械や設備、物などが不安全な状態であることを指し、事故や労働災害が発生しやすいもしくは、発生する原因が作り出されている状態のことです。
作業の安全性を脅かす原因として、不安全行動が人にあるのに対し、不安全状態は環境にあるのが大きな違いです。
不安全状態の類型
不安全状態とは、作業環境や設備そのものが事故の要因となる物理的なリスクを指します。厚生労働省では以下の8つに分類されています。
- 物自体の欠陥
- 防護措置・安全装置の欠陥
- 物の置き方、作業場所の欠陥
- 保護具・服装等の欠陥
- 作業環境の欠陥
- 部外的・自然的不安全な状態
- 作業方法の欠陥
- その他
例えば、老朽化した設備の放置や滑りやすい床材、整理整頓が行き届いていない現場などは、すべて不安全状態の例です。作業者の安全意識だけでは防げないリスクであり、設備管理者や企業全体での継続的な点検・改善が求められます。
不安全行動と不安全状態は重なって労働災害が発生することが多い
不安全行動と不安全状態は、単独で起こるよりも、実際には重なって労働災害を引き起こすケースが多数あります。例えば、機械の安全装置が故障したまま放置されていた(不安全状態)状況で、作業者がその装置を確認せずに操作した(不安全行動)というように、原因が連鎖して重大事故につながることが少なくありません。
厚生労働省の統計でも、労働災害の発生原因のうち、不安全な行動および不安全な状態に起因するものが94.7%と高い割合を占めています。
どちらかを是正しても、労災リスクは完全には取り除けないため、安全対策を講じる際は、作業者の安全教育と同時に現場環境の点検・改善にも取り組み、「人」と「環境」の両軸を見直すことが大切です。
なお、設備の点検・改善は時間や費用が発生するため、まず取り組むべきなのは、従業員の安全意識向上です。安全意識が向上することで、不注意や思い込みによる不安全行動が削減され、労働災害につながるリスクも抑えられます。
安全教育を進めるにあたっては、労働安全コンサルタントとして労働安全衛生問題に取り組んできた鈴木 孝氏による解説動画の視聴がおすすめです。「安全衛生教育を実施しても労働災害が発生してしまう理由」「従業員の安全意識が継続する教育方法」などを解説しています。視聴は無料ですので、下の画像をクリックして動画をご視聴ください。
不安全行動が由来の労働災害は非常に多い
労働災害の発生原因の多くは、実は現場での「不安全行動」に起因しています。
厚生労働省「労働災害を防止するために」によると、労働災害のうち「不安全な行動」および「不安全な状態」が関与するケースはそれぞれ9割を超えており、両者が同時に存在するケースが全体の約8割にものぼるとされています。つまり、現場でのヒューマンエラーや危険な行動が、災害発生の引き金となっているのです。
製造業や建設業、農業などでは、高所作業や傾斜地での作業といった「不安全な状態」も重なり、より重大な労災へとつながるリスクが高まります。不安全行動と不安全状態が接触することで災害が発生するという構造を理解することが重要です。
不安全行動を減らすためには、作業手順の明確化、安全教育の実施、KY(危険予知)活動など、日々の積み重ねが欠かせません。職場全体で安全文化を醸成し、従業員の「安全を守る意識」を根付かせることが、労災を減らすためには大切です。
不安全行動によって発生した労働災害の事例
ここからは、不安全行動によって発生した、厚生労働省「職場のあんぜんサイト」に掲載されている労働災害の事例を紹介していきます。
【製造業】切削作業中に回転中の鉄棒に手が巻き込まれた
金属加工を行う事業場にて、旋盤による鉄棒の切削作業中に災害が発生した事例です。被災者は、機械が稼働している最中に横送り台の上に置かれていた注油用容器を手で取ろうとした際、回転中の鉄棒に作業服の袖が巻き込まれ、結果として手首を切断する重傷を負いました。
原因として考えられるのは以下のとおりです。
- 注油容器の配置場所が定められておらず、作業者が危険箇所に物を置いていた
- 安全衛生推進者はいたものの個々の労働者に対する安全教育が徹底されていなかった
- 作業者自身の長年の経験からくる「慣れ」や過信
これらの原因を踏まえたうえで講じられる対策は、作業服の正しい着用、そして定期的な安全教育の実施などが挙げられています。慣れによる油断が命取りとなるため、日々の作業においても基本の徹底と教育の継続が大切です。
参考元:厚生労働省 職場のあんぜんサイト 【旋盤にて鉄棒の切削作業中、回転中の鉄棒に手が巻き込まれた】
【運送業】カゴ台車が倒れ下敷きになった
道路貨物運送業の構内作業中、カゴ台車が転倒し作業員が荷物の下敷きとなり死亡するという痛ましい労働災害が発生しました。
事故の背景には、台車上部に長尺・重量物を積載するという危険な作業方法が日常的に行われていたという職場の慣習があります。上記の行為は同事業所が作成していた「長尺物の荷扱いマニュアル」で明確に禁止されていたものの、ルールが形骸化して現場で守られていませんでした。
再発防止には、第一に「荷物の大きさ・重さに適した運搬機材を使用させる」ことが必要です。また、マニュアルの実態に即した見直しと、それにもとづく現場教育の徹底も求められます。形式的なマニュアルや教育では命は守れません。運送業に限らず、「ルールを守る文化」を根付かせることが、安全な職場づくりには大切です。
参考元:厚生労働省 職場のあんぜんサイト【カゴ台車が倒れ下敷きとなった】
【飲食業】厨房において、濡れた床で転倒した
ファミリーレストランの厨房内で、被災者が床にこぼれた水に足を滑らせ転倒し、事故直後は軽傷と思われていたものの、翌日に容体が急変し、死亡に至った事例です。
床が濡れた状態で放置されていたことが直接の要因ではあるものの、被災者は耐滑性のある靴を要望していたにも関わらず、事業者がその対応を怠っていたことも大きな要因です。このような災害を防ぐには、濡れた床の即時清掃はもちろん、耐滑靴の支給や滑りにくい床材の採用、安全衛生教育の徹底が不可欠です。
参考元:厚生労働省 職場のあんぜんサイト【飲食店の厨房において、濡れた床で転倒して死亡した】
【建設業】ビル内の配管の撤去作業中、爆発が発生
解体中のビルの配管撤去作業中、ガス臭が漂ってきた中で作業を続けていたところ、建物内に滞留していたガスに引火して爆発が発生し、3名が熱傷を負った事例です。
爆発した要因は、作業開始前に「ガスの供給状況を正式に確認しなかった」ことに加え、ガス臭という明確な異常を感じながらも作業を中断せず、防爆構造でない電動工具を使用したことです。
再発防止策としては、事前にガスの供給元との連携による確認の徹底、可燃性ガスの検知器を使用しての作業再開判断、防爆構造の工具の使用の徹底が必須です。また、現場のKY活動や安全施工サイクルの実施、リスクアセスメントの実施などが不可欠です。
参考元:厚生労働省 職場のあんぜんサイト【ビル解体工事において、ビル内の配管の撤去作業中、爆発が発生し、熱傷を負った】
不安全行動をなくすには?発生を防ぐための具体的な対策
不安全行動は重大な労働災害の原因となります。具体的に以下の7つの対策を講じることで、現場のリスクを根本から減らせます。
- 労働者への安全教育を実施する
- 従業員が作業ルールを守れる作業手順書を作成する
- 不安全行動の要因を把握して排除する
- KY活動を実施する
- チェックリストを作成して作業前の記入を仕組み化する
- 労働災害を疑似体験させる
- 指差呼称を徹底させる
労働者への安全教育を実施する
安全教育は、すべての対策の基本です。転倒事故や機械巻き込まれ事故の背景には、作業者の危険認識の甘さや教育不足が原因となります。特に新規雇用時や業務変更時には、法律でも教育が義務付けられており、繰り返しの実施が求められます。一度限りの講義ではなく、動画やイラストを用いた実践的な教育、現場での声かけ・指導の継続によって、知識と行動の定着を図りましょう。
安全意識を形骸化させないためにも効果のある安全教育を実施するのが大切です。以下の動画では、労働安全コンサルタントとして労働安全衛生問題を解決してきた専門家による「安全意識を形骸化させない安全教育の進め方」を解説しています。無料で視聴できるので、不安全行動をなくすための参考としてぜひご覧ください。
>>安全意識を形骸化させない安全教育の進め方を見てみる【視聴無料】
従業員が作業ルールを守れる作業手順書を作成する
事故が多発する背景には「形だけの手順書」が存在することが少なくありません。作業手順書は現場実態に即した内容であることが大前提。作業者の声を取り入れ、無理なく守れるルールを構築し、視覚的に分かりやすく提示することで、安全な行動を自然に選べる環境づくりを目指しましょう。
実際に安全教育が定着しないと悩みを抱えていた「ASKUL LOGIST株式会社」では、作業手順書の作成や整備によって、誰が作業を行っても安全に、かつ一定水準の品質のものを効率よく実現ができたと効果を実感しています。
同社の具体的な取り組みは、紙の手順書から動画を活用した手順書の作成です。従来の教育だけでは受け手側の解釈で理解がバラついてしまう中でも、動画にすることで作業の標準化・安全教育を浸透させることができています。
同社の事例を詳しく読んでみたい方は、インタビュー記事をご覧ください。
>>ASKUL LOGIST株式会社のインタビュー記事を読んでみる
不安全行動の要因を把握して排除する
不安全行動を引き起こす原因を把握せずに注意だけを繰り返しても、根本的な解決にはなりません。長年の慣れ、過信、時間的なプレッシャーなど、背景には複雑な事情があります。
特に「危ないとわかっていてもやってしまう」行動に対しては、ルールの再設計や意識改革に取り組み、作業者と対話しながら、実効性ある対策を打つことが大切です。要因を洗い出す上で大切なのが、不安全行動の要因に対して、「なぜ?」を繰り返し掘り下げる「なぜなぜ分析」を活用してみてください。
なぜなぜ分析についてより詳しく知りたい方は、なぜなぜ分析を提唱したトヨタにて、訓練指導者である「伊藤正光氏」のセミナーの様子をまとめた以下の資料をご覧ください。
>>【事例で解説】トヨタ流「なぜなぜ分析」の実践方法とポイント(解説動画あり)を見てみる
KY活動を実施する
KY(危険予知)活動は、作業前にリスクを洗い出し、事故を未然に防ぐための基本です。爆発事故や転倒事故のような重大災害も「事前に気づいていれば防げた」はずのケースが多く見られます。
作業内容の共有から危険ポイントの確認、対応策の立案、指差し唱和まで、チーム全体で行うプロセスが現場の安全意識を高めます。形式に流されず、実効性のあるKYを定着させましょう。
KY活動の進め方がわからない方は、KY活動の目的や1人でできるKY活動、4ラウンド法の進め方などを解説している以下の解説動画をご覧ください。
>>「元労基署長が解説!事故を未然防止するKY活動と4ラウンド法の在り方とは?」を見てみる
チェックリストを作成して作業前の記入を仕組み化する
作業前の確認を「個人任せ」にせず、チェックリストという形で仕組みに落とし込むことが重要です。『不安全行動によって発生した労働災害の事例』で紹介した、厨房での転倒事故や構内作業での荷崩れ事故は「ほんの少しの確認」があれば防げた事例です。
項目は簡潔かつ具体的にまとめ、作業者が自分で点検しやすいよう工夫することがポイント。毎日の習慣として根付けば、リスク回避の精度が大きく高まります。
労働災害を疑似体験させる
現場での危険を「体感」してもらうことは、安全意識を育てる上で非常に効果的です。実際に事故を経験する前に、その怖さを疑似体験できる研修や教材を活用しましょう。
例えばアニメーションやシミュレーション映像などを使えば、若手や新人にも直感的に伝わりやすくなります。単なる注意喚起ではなく、「もし自分がその場にいたら」と想像させることが、行動の変化につながります。
指差呼称を徹底させる
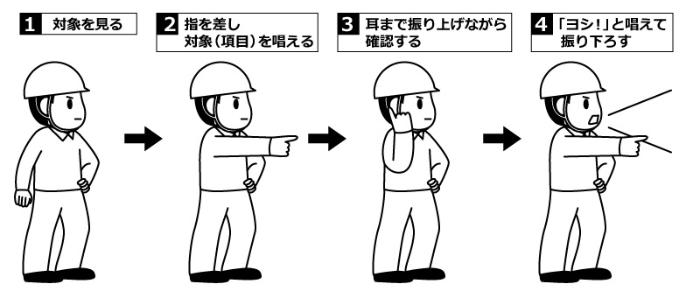
引用元:中小建設業特別教育協会『安全確認のための「指差し呼称」』
「確認したつもり」を防ぐには、視覚と声で意識を強化する指差呼称が効果的です。現場での些細な見落としや判断ミスが、大きな事故を引き起こすケースは後を絶ちません。
「○○ヨシ!」と声に出して確認することで、動作の確実性が高まり、周囲への警告効果も生まれます。単調な作業こそ危険が潜んでいます。日々の作業に自然に組み込み、習慣化させることが大切です。
不安全行動の削減を実現している企業事例と取り組み
ここでは、実際に不安全行動の削減を実現している企業の具体的な事例、その事例から分かる有効な取り組みなどについて紹介していきます。
安全意識を高め、不安全行動を減らしている事例2社
不安全行動を減らしている事例として以下の2社を紹介します。
- ASKUL LOGIST株式会社
- 児玉化学工業株式会社
ASKUL LOGIST株式会社
ASKUL LOGIST株式会社は、アスクル株式会社の物流業務を担うグループ企業として、全国15拠点に物流センターを構えています。外国籍労働者や短時間勤務者、障がい者など多様な人材を積極的に採用しており、紙の手順書やOJTなどの従来の教育方法では、伝達のばらつきや理解の難しさが課題となっていました。
そこで同社では、紙で作成していた手順書を動画マニュアル作成ツール「tebiki現場教育」を活用して動画の手順書を作成。導入時教育や安全教育を映像で可視化することで、理解の均質化と標準化を実現しています。
また、新人教育の時間も2時間から30分に短縮され、教育工数の削減と教育内容の定着が図られました。動画制作は現場スタッフと共に改善を重ねながら進められ、教育体制全体の質向上と継続的な改善文化の醸成にもつながっているとのことです。同社の詳しい事例を読みたい方は、以下のインタビュー記事をご覧ください。
インタビュー記事:従業員数3,500名超・全国15拠点で動画マニュアルtebikiを活用!
児玉化学工業株式会社
1946年創業の化学メーカーで、自動車部品や住宅設備、エンターテインメント分野におけるプラスチック成形を手掛けている児玉化学工業株式会社。
同社の製造現場では500以上の要領書が存在し、外国籍従業員も多く在籍する中で、紙のマニュアルでは動きやニュアンスが伝わらず、作業のばらつきや製品不良が発生するという課題を抱えていました。
こうした課題に対し、紙のマニュアルから動画マニュアル作成ツール「tebiki現場教育」を活用して、動画マニュアルを作成し、誰にでもわかりやすく、視覚的にルールや手順を伝達できる環境を整備。手順書作成の工数も紙の1/3に削減され、教育の均一化と習熟の迅速化が進みました。動画による教育は、社内全体のルール共有や品質向上にも寄与し、将来的には全工場への展開を目指しています。同社の詳しい事例を読みたい方は、以下のインタビュー記事をご覧ください。
インタビュー記事:手順書作成の工数は紙の1/3になったと思います。
不安全行動の排除に効果的な取り組み
不安全行動を根本から排除するには、単なる注意喚起や叱責では不十分です。効果的な取り組みとして、「現場実態に即した作業手順の明文化」「従業員への定期的な安全教育」が欠かせません。
これらの2つをサポートするのが、動画を活用したマニュアルの作成です。動画マニュアルの作成~活用によって、言語や経験の壁を超えて作業手順やルールを伝えることができ、従業員ごとの理解度も統一できます。
実際にtebiki現場教育を利用している株式会社ロジパルエクスプレスでも、「動画を見ておいてもらうだけでも安全品質意識を担保できている」と実感しており、不安全行動の防止につながる安全意識の向上も期待できます。
tebiki現場教育の機能や特徴、導入後のサポート体制などをより詳しく知りたい方は、以下のサービス資料をご覧ください。
不安全行動の削減に努めよう【まとめ】
不安全行動は、労働災害につながることもある危険な要因になるため、従業員の不安全行動をさせないための意識改革や安全教育が非常に重要です。
しかし、従業員の安全意識を向上させるのは難しく、形骸化してしまうケースも多いため、自社の実態に即した対策が必要になります。その対策の1つとして有効なのは、動きやルールを視覚的に伝えられる動画マニュアルの活用です。
不安全行動の排除に、本記事でご紹介した「tebiki現場教育」を活用してみたい方は、以下の画像をクリックして資料をご覧ください。