かんたん動画マニュアル作成ツール「tebiki現場教育」を展開する、現場改善ラボ編集部です。
海外に事業展開している製造業や企業からは、「海外工場での品質管理は難しい」という声をよくうかがいます。
文化や習慣、歴史、人生観といった多くの点が日本とは異なるため、日本流をそのまま押し付けても現場がうまく機能しないケースが少なくありません。また、言葉の違いによるミスコミュニケーションや、作業マニュアルが正しく理解されないという課題も目立ちます。
そこでこの記事では、海外工場における品質管理が難しい原因を紐解くとともに、その課題策について解説します。
目次
海外工場の品質管理、なぜ難しい?よくある4つの課題
国内工場と比較したとき、海外工場の品質管理が難しいとされている理由をまずは解説します。
文化・習慣の違いによる品質意識のずれ、作業手順の不遵守
海外工場での品質トラブルは、多くの場合、人為的なミス(ヒューマンエラー)によって起きています。なぜでしょうか?それは、「品質に対する意識の違い」が挙げられます。
日本人は基本的に、丁寧に、美しく仕上げることが「良い仕事」だと考えます。買った人が気持ちよく使ってくれるようなモノを届けたいと考えて、丁寧な仕事をする傾向にあるのです。
そのため、例えば作業手順書で細かいことまで書かれていなくとも、線に沿って切るのが当たり前だし、見栄え良く仕上げることも「当たり前」として作業をするのが日本人の傾向です。
しかし、海外工場ではその「当たり前」がまったく通じません。手順書に書かれていないことは自由に作業します。効率よく、簡単にできるなら、作業手順も勝手に変えて進行します。
その結果、生産された製品は「想定されている性能が出力されない」「設計寸法通りに仕上がっていない」といった品質トラブルを引き起こすことになるのです。
言語の壁によるコミュニケーション・教育の難しさ
日本国内と海外の生産拠点では、同一製品であっても最終的な品質や仕上がりに差異が生じることがあります。それは、作業手順書を現地語へ翻訳する際に、以下のようなアクシデントが発生するケースがあるからです。
- 原文の細かなニュアンスが失われるから
- 不正確な翻訳がなされるから
さらに、このような作業上の差異を指摘し是正しようとしても、言語的な障壁によって指示を的確に伝達できず、問題の完全な解消を困難にするケースも少なくありません。
この課題は製造業に限定されるものではなく、例えば飲食店や小売店といったサービス業においても散見されます。海外店舗では接客応対の標準化が難しく、結果として国内店舗とは異なるサービス品質や店舗運営を提供してしまうことがあるのです。
また、OJTなど現場教育の質の担保も難しく、従業員のスキルのばらつきが大きくなりがちな側面もあります。
加えて、多国籍の従業員が混在する現場では、円滑な意思疎通が難しいため、日本国内の現場と比較すると「報告・連絡・相談」といった基本的なコミュニケーションが頻繁に行われないという現実があります。その結果、従業員が不明点を自己判断で解釈して作業を遂行してしまい、結果としてマニュアルや標準作業とは異なる作業フローが定着してしまうのです。
例えば、アメリカに工場拠点を持つ株式会社Archemでも同様の課題を以前抱えていました。
私が管轄しているテネシー工場では、チームメンバーが紙の作業指示書を読み、その後実際に仕事を行う様子をトレーナーが見てフィードバックするという体制で教育を行っていました。母国語が英語以外の一部のメンバーは、英語の作業指示書を読めないため、その場合にはOJTのみで指導をするという体制になります。
細かい作業やカンコツ作業が多いため、英語が話せる方でも「紙の作業指示書の内容を実際の作業工程に落とし込んで理解する」ということが難しいようでした。
同社が言語の壁を乗り越え、品質向上を実現した詳細な事例は以下のインタビュー記事でご覧いただけます。
インタビュー記事:アメリカ3工場にて言語の壁を乗り越え、製品品質と生産性を向上
人材の流動性が高く、スタッフや作業者が頻繁に変わる
日本では、企業に就職すると「同じ場所で長くキャリアを築こう」とする方が多く、頻繁に仕事を変えることについては、どちらかというと慎重な見方がされがちです。1つの組織に長く貢献することが美徳とされる風潮も完全にはなくなっておらず、そうした背景から、日本企業はじっくりと時間をかけて人材を育成しやすい環境だと言えます。
一方、海外では1つの場所で勤め上げるというよりは、スキルを磨き、経験を積んだら、それを活かせるより魅力的な次のステージへと積極的に移っていくのが一般的なスタイルです。特に若い世代ではこの傾向が顕著で、企業側からすると、時間をかけて育てた人材が、ようやくこれからという時に転職され、また新たな人材を1から教育し直すというループに陥り勝ちです。
従業員の入れ替わりが頻繁になると、どうしても業務のノウハウや「暗黙知」といったものが組織に蓄積されにくく、結果として製品やサービスの品質にばらつきが生じやすくなるのです。
サプライヤー品質のばらつきと管理の難しさ
モノやサービスのばらつきは生産工場内の仕事だけに限りません。現地調達する部品のばらつきも日本より大きいため、組み立てた時に隙間が生じたり、バリや異物がついていたり、完成品の質がばらつきやすくなります。
図面や仕様書の公差内であればよいと考えて、連絡なしに工程を変えたり、材料を変えたりして部品を納入するサプライヤーもいます。
物流面でも国内輸送だけとは限らないため、通関に時間がかかったり、荷物の積み下ろしが雑で部品にダメージがあるなどのトラブルがあり得ます。性善説に基づいた管理が通用しないため、常にリスクを考慮した品質管理が求められます。
品質管理の難しさから引き起こされる品質リスク
ここまで、海外工場では品質管理が日本工場と比べて難しい理由や課題について解説しました。では、そうした課題を解消できないとどのような問題が生じるのでしょうか?
コミュニケーション不全による原因究明の遅れや誤り
お客様に製品やサービスを提供していると、ときにはスペック外れの商品を納入してしまったり、注文とは異なる商品を納入してしまうというトラブルが発生します。そのとき、スピーディに解決するためには早く原因を見つけ、それを取り除くことが重要です。また、正しいものを代納したり、返金に応じたりして、お客様の不安や不満を取り除くことも必要です。
国内であれば、誰が何をするかをすぐに指示をして、役割分担をすることで早期の解決を図ることができますが、海外工場では言葉の壁があって指示がうまく伝わらず、対応が遅れてしまう場合があります。また、指示内容の誤解により、誤った対応が発生するなど、トラブル時のミスコミュニケーションが原因で、顧客信頼を失ってしまうリスクがあります。
品質意識・文化の違いによる不良の多発・再発
日本工場であれば出荷されないレベルの外観不良品が、海外工場の場合は「これくらいの不良であれば出荷しても問題ないだろう」という判断がなされ、不良品が最終検査をパスして出荷ロットに混入したり、顧客に流出してしまうことがあります。
また、問題に気づきながら、報告したら面倒になるという気持ちからそのまま放置して、トラブルが再発したり、多発してしまったりします。その結果、顧客の信頼を失い、受注が減ってしまうリスクがあります。
力量の変化により製品の質、サービスの質が変わり客離れが起きる
老舗の料亭で、板前さんが変わったら味が落ちて人気がなくなってしまった、という話がよくあります。
工場も同じように、作業者やスタッフのスキルに依存したモノづくりをすると、製品の品質、サービスの品質が落ちて評判が下がったり、クレームが増えたりしてしまいます。その結果、顧客からの信頼を失って注文をいただけなくなります。
特に海外工場の場合、より良い条件の職場があれば転職するのが当たり前なので、時間をかけて教育した社員がやめてしまい、常に中堅社員が不足している状況です。トレーナーと新人しかいないため、組織の力量バランスが不安定で、組織力が向上したと思ったらメンバーの異動や転職により、また振り出しに戻るということが起きます。
海外工場の品質管理・改善を進める3つの対策例
ここまで、海外工場の品質管理がうまく推進されない課題や、その先に生じる問題について解説しました。
では、海外工場の品質管理を改善するための対応策は何が挙げられるのでしょうか?
品質管理体制の強化と「電子化」
現在、多くの企業がDX化を進めています。作業効率や生産性の向上のための自動化、ロボット化と並んで、品質管理面でもデジタルトランスフォーメーションに大きな期待が寄せられています。
品質データの収集・分析体制の構築(デジタルツールの活用)
生産計画の進捗や作業記録は、まだまだ「手書き」「紙の帳票」で記録されている現場が多いです。これらは記録としては残すことはできますが、「データ活用」まで応用することはできません。
そこで、現場帳票を電子化(デジタル化)して記録を残せるようにすると、生産遅延の起きやすい工程や、不良率が高い問題工程がどこかを分析することができるようになります。
たとえば、工程のInからOutまでを工程別にタイムチャートにしてみたり、パレート図を描いて時間のかかる工程順に並べてみると、容易に問題個所が抽出できるようになります。そして、日本の工場と海外工場の違いを比較してみると、海外工場でトラブルが起きやすい作業が見えるようになるのです。
関連記事:現場帳票を電子化する方法と主要ツール比較!システムの選び方は?【事例やメリットも解説】
不良率、手直し工数、クレーム件数などのKPI設定とモニタリング
プロセスの有効性と効率は、ベンチマークとする指標(KPI:Key Performance Indicator)と目標値を設定してモニターし、それを定期的にレビューすることで確認できます。たとえば、期初に立てた工程不良率目標に対して現時点で達成できているのかや、手直しにかかる工数が従来よりも増えていないか、顧客クレームは減少しているかなどを毎月確認するのです。
KPIの推移をグラフ化して視覚的にわかるようにしたり、不良の内訳を国内工場と比較するなどして、海外工場が現在抱えている課題をいち早く抽出し、安定した生産が続けられるようにフィードバックをします。
指標の可視化の例として、かんたんデジタル現場帳票「tebiki現場分析」では、以下のように帳票の記録を自動でグラフ化します。
-1024x576.png)
不良数・不良率の月次推移ダッシュボード(tebiki現場分析)
このように、現場帳票のデジタル化(データ化)を通じて工場の現状を見える化することで、現状の課題とそれに対する打ち手をデータから迅速に導き出すことが可能になります。
帳票のデジタル化を推進する方法について知りたい方は、以下の資料「はじめての現場帳票デジタル化ガイド(pdf)」が参考になると思います。あわせて参考にしてみてください。
>>>「はじめての現場帳票デジタル化ガイド(pdf)」を見てみる
コミュニケーションの壁を乗り越える工夫
海外工場における言語の壁を低くし、円滑なコミュニケーションをしやすくするための工夫として、以下のような取り組みが進められています。
図や写真、動画など、視覚的な情報伝達手段の活用
言葉や文字による説明よりも、図や写真、動画といった「視覚的な情報伝達」を活用しましょう。目で見ることで、色、形、現場の雰囲気が情報として入ってきますし、手の動かし方、体の姿勢なども真似しやすくなります。
例えば、タイに所在地のあるHOEI THAILAND CO.,LTD.では、100ページ以上に及ぶ紙マニュアルに教育の限界を感じ、動画による教育体制を整備しました。紙マニュアルは作業手順の理解が非常に難しく、従業員が独り立ちするまでに5か月はかかっていたのです。
そこで動画マニュアルを導入し、作業手順を視覚的に分かりやすく教育することに成功しています。以下の動画は、同社で実際に活用されている動画マニュアルのサンプルです。
▼海外工場で活用されている動画マニュアル例▼
※「tebiki」で作成
字幕も1ボタンで母国語に変換しているため、翻訳工数もかかっておらず、外国人教育に適した教育ツールとなっています。
同社の動画マニュアル導入による、現場教育の詳細事例については、以下のインタビュー記事で紹介されています。あわせて参考にしてみてください。
インタビュー記事:動画を活用した不具合対策により ダウンタイム短縮を実現
文化や習慣の違いを意識して、現地の価値観に合わせた品質の重要性を説明する
「日本ではこうだった」「日本工場ではこう作業する」という説明は、海外工場で働く人の心には響きません。国の歴史や現在の政治状況、生活習慣がまったく異なるため、共感が得られにくいのです。その国の実情や価値観を考慮しながら、1番理解してもらいたい品質の重要な部分を言葉を工夫して説明します。
特に、品質を向上することでローカルスタッフや作業者自身にどのようなメリットがあるのか、よい未来をイメージできるように説明することが効果的です。
多言語対応ツールの導入
海外工場の立ち上げ支援や工程維持、改善のために出向する担当者全員が、同じレベルの言語能力を持っているわけではありません。英語や中国語が流暢に話せるとは限らず、知っている単語の数も異なるため、コミュニケーション能力にばらつきがあります。
そこで、翻訳ツールの活用を検討しましょう。昨今はAI技術が急速に発達し、言葉のニュアンスを考慮した翻訳、通訳をしてくれるようになりました。また、多言語対応により、英語や中国語といったメジャーな言語だけでなく、海外工場のあるローカル言語(たとえばベトナム語、タイ語など)に変換してコミュニケーションを図ることもできます。
「守られやすい」作業標準の整備と運用の徹底
人による作業のばらつきをなくし、安定した品質の製品を作り続けるためには、作業標準の整備が重要です。しかし、作業標準を整備しても、現場で守らなければ意味がありません。そこでここでは、作業標準が守られるための工夫や取り組みについて紹介します。
なぜそのルールが必要なのか、背景や目的を丁寧に説明する
作業手順が単に書かれた手順書は、作業者ごとに解釈の違いが生じやすいです。特に海外工場の場合、作業者が勝手に、より簡単でスピーディーにできる作業に置き換えてしまう恐れがあります。その結果、本来の狙いと異なる作業をしてしまい、品質のばらつきや、設計から外れた製品を生み出す原因になります。
そうならないよう、作業手順書には、作業手順だけでなく「どのような状態に仕上げることを目的としているのか」「なぜその作業手順を守らなければならないのか」「もし守らないとどのような不具合が起きるのか」を丁寧にまとめましょう。
作業手順を守る必要性を、背景や目的を交えながら説明することで、現場全体で標準化が浸透していきます。
動画で手順を示すことで、理解度を高め、作業遵守を促す
スムーズな教育の第一歩は、やって見せることです。言葉で説明しても想像する内容が作業者間で異なるため、作業のばらつきが生じやすくなります。とはいえ、作業者ひとりひとりにOJT教育を実施するのは、時間の確保が難しく現実的ではありません。
そこで有効となる手段が動画による教育です。正しい作業手順を動画におさめ、現地の教育フローに組み込むことで、疑似的な「やって見せる」教育が可能になります。手の動かし方、安全に作業するための姿勢、確認するポイントなどを動画を使って説明することで、理解度を高めます。
例えば、自動車部品や住宅設備等のプラスチック成形品を手掛ける製造企業である児玉化学工業株式会社では、現場従業員が以下の動画マニュアル「ヤスリでバリを取る業務プロセスの解説」を作成し、技術をスムーズに共有しています。
▼動画マニュアルによる技術継承の例(音量にご注意ください)▼
※現場従業員が「tebiki」で作成
一目で「何をどうすればいいか」が把握でき、文字では伝えにくい動きもすべて理解できるようになっています。実際、同社の現場では外国人スタッフが多く、スペイン語、ポルトガル語、中国語、ベトナム語などさまざまな言語が飛び交っている環境です。そのため動画のような非言語教育ツールが必須でした。
上記のバリ取りのような作業手順を文字で説明するには多くの情報量が必要ですが、動画であれば、正しい作業手順が一目でわかります。誤翻訳によるミスコミュニケーションを減らすには、動画のような「視覚的に理解しやすい情報伝達」の整備が有効手段です。
製造業では動画による現場教育の改善事例が徐々に増えてきているので、それらの事例もあわせて知りたい方は「製造業における動画マニュアル活用事例集(pdf)」も参考にしてみてください。製造業の動画マニュアル活用事例が多数収録されているので、自社で動画マニュアルを導入する際の具体的なイメージがしやすいはずです。
>>>「製造業における動画マニュアル活用事例集(pdf)」を見てみる
OJTトレーナーの育成と指導方法の標準化
品質のばらつきを解消するには、作業者の手順標準化だけでなく、「指導者の教育内容」も標準化しなければなりません。というのも、OJT教育が重要な製造業では、OJT担当者の教育内容にバラつきが生じがちだからです。
「誰が教えても同じ教育内容」を実現するには、前提として、「従業員が習得すべきスキル」「従業員が習得できているスキル」を可視化し、一覧化できていなければなりません。これらを整えるのに有効なのが「スキルマップ」です。
スキルマップとは、従業員が持つ技術とレベルを可視化し、今後取得してほしい技術を整理できるスキル管理のツールです。以下のサンプルのように、人材とスキルを表形式で管理できるもので多くの製造現場で活用されています。
表-1024x479.png)
現場教育を進めるときには、現段階のスキル保有状況を可視化し、誰にどの技術を伝えるべきかを整理できると理想であるため、スキルマップを活用した教育訓練計画が有効です。
また従業員視点でも、どのスキルを取得すると評価につながるか?という点が可視化されるようになります。
とはいえ、スキルマップの運用が続かず形骸化している製造現場は少なくありません。紙による管理が煩雑で、気が付けば最新状態に更新されていないというケースが多いです。そこで推奨したいのが、「クラウド型スキルマップ」の導入です。
例えば、製造現場に特化したクラウド型スキルマップ「tebiki現場教育」では、下図のように「従業員ごとのスキル習得状況」を可視化します。
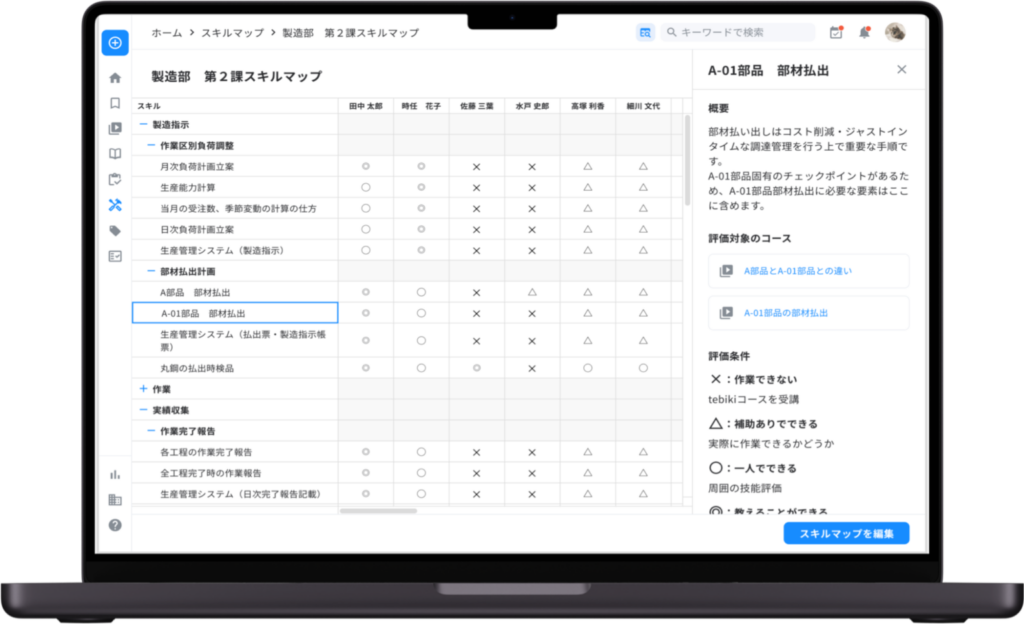
【「動画マニュアルが紐づくクラウド型スキルマップ – tebiki現場教育」より抜粋】
tebiki現場教育の詳細機能や活用事例について詳しく知りたい方は、以下のPDF資料もあわせてご覧いただくと、tebikiを現場でどのように活用できるのか・どのように稼働率向上に貢献するのかが具体的にイメージできます。
>>>PDF資料「動画マニュアルが紐づくクラウド型スキルマップ『tebiki現場教育』」を見てみる
海外工場の品質改善を実現している事例
海外工場の品質改善に成功している製造業事例を紹介します。自社での品質改善の参考にしてみてください。
HOEI THAILAND Co.,LTD.の成功事例(タイ)
HOEI THAILAND社は、食品用の包装資材をつくるメーカーです。卵豆腐用のチューブ型フィルムパックやクラフト内装紙などを製造しています。
同社では以前、教育ツールとして100ページになる紙マニュアルを使用していました。そのため、新人が内容を理解するだけでも大変で、独り立ちするまでに5ヶ月かかることもありました。また、教育する人によって教え方や内容が異なるため、品質にムラが生じていただけでなく、教育を受ける側が混乱してしまったり、トラブル時の問題箇所の特定に時間がかかってラインダウン(ライン停止)にまで発展してしまうこともあったそうです。
これを解決するために、現場教育に「動画マニュアル(tebiki現場教育)」を導入したところ、実際の作業を見ながら実習できるため作業者の理解が深まり、新人の立ち上げ期間が1ヶ月に短縮できました。
また、作業内容を細分化して教育できるため、トラブル発生時も臨機応変できるようになり、ダウンタイムも解消されました。そして、わからなくなった作業はトレーナーに聞かなくても作業者自身が動画マニュアルを何度でも見ることができるため、標準作業の定着を図ることもできています。
同社の詳しい改善事例については、以下のインタビュー記事からご覧いただけます。あわせて参考にしてみてください。
インタビュー記事:動画を活用した不具合対策によりダウンタイム短縮を実現
株式会社Archemの成功事例(アメリカ)
株式会社Archemはシートパッドや産業化成品を製造するメーカーです。アメリカ国内に3つの工場を展開して、多国籍な従業員が働く職場です。
同社のアメリカ工場では、英語を母国語としない作業者にはマニュアルだけでは教えきれず、OJTで実作業を教える必要があります。その時、紙のマニュアルに書かれている内容を、実作業に落とし込むことが難しく、とくにカンコツを伝えることに苦労されていました。
また、転職が多く、せっかく教育した作業者がやめてしまったり、トレーナー自身も他社へ移っていなくなってしまうなど、継続的に均質な教育ができないという課題も持っていました。
そこで動画マニュアル(tebiki現場教育)を導入してこれらの課題を解決しました。現場では同じ作業の繰り返しでは作業員が飽きてしまうため、作業のローテーションを組み込んでいますが、常時モニターに作業動画を映しているため、作業者が確認してから作業を開始することができ、品質のばらつきが改善されています。
同社の詳しい改善事例については、以下のインタビュー記事からご覧いただけます。あわせて参考にしてみてください。
インタビュー記事:アメリカ3工場にて言語の壁を乗り越え、製品品質と生産性を向上
海外拠点で活用事例もある教育改善ツール
海外拠点の事例から、言語の壁によるコミュニケーションの難しさや、転職が多いことによるスキル維持の難しさなど、日本とは違った課題があることをおわかりいただけたと思います。多言語対応、わかりやすいマニュアル、教育のしやすさが、海外工場での品質管理を成功させる鍵です。
活用事例でも紹介されていたように、動画マニュアルはこれらの課題を解決できる有効な手段です。1から10まで言葉による説明がなされなくとも、一目である程度の作業内容が理解できるのが動画マニュアルの強みであり、「誰が教えても同じ教育内容」になることから、品質のバラつきが解消されるツールでもあります。
動画マニュアルの導入に少しでも興味がある方は、現場に動画マニュアルを導入するには具体的に何をどう推進すればいいのか、気になると思います。そこで、資料「はじめての動画マニュアル作成ガイド(pdf)」では、現場教育に動画マニュアルを組み込むための推進方法についてまとめられているので、あわせて参考にしてみてください。
下の画像をクリックすると、資料をダウンロードできます。
まとめ
海外工場での品質管理は、コミュニケーションをいかに円滑に行えるかが成否を分けます。問題が発生したらすぐに関係するスタッフに情報共有を行い、原因究明と対策の議論が行われることが重要です。言葉で伝えるだけではなく、図や写真、動画など目で見える情報を活用することで、言語の壁を克服することができます。
わかりやすい教育ツールを使えば正しい作業を遵守できて、異常があった箇所をいち早く発見することができるようになり、再発防止のためのアイデアも出やすくなります。また、新人の独り立ちが早くなり、職場メンバーのスキルレベルを維持し、製品やサービスの品質維持に役立ちます。
tebiki現場教育の動画マニュアルは、海外工場における品質管理の課題を解決する手助けができます。ぜひ一度、検討してみてください。