物流に特化した動画マニュアル作成ツール「tebiki現場教育」を展開する、現場改善ラボ編集部です。
危ないことが起きたものの、幸いにも事故や災害には至らなかった事象を「ヒヤリハット」といいます。倉庫や物流の現場には危険が多く、些細なミスや不注意が深刻な事態を招くことにもなりかねません。日常の中にある小さな異常や違和感を見逃さずに対策を講じ、重大な事故や労働災害を未然に防ぐことが重要です。
本記事では、倉庫・物流作業におけるヒヤリハット事例を紹介します。労災発生を防ぐ具体策や企業事例もまとめていますので、倉庫や物流現場での安全対策にお役立てください。
以下の資料では、ヒヤリハットが発生した際にそのまま使える報告書のテンプレート、ヒヤリハットの具体的な再発防止策について詳しく解説していますので、本記事とあわせてご利用ください。
>>「イラストでわかりやすい!報告から教育まで行えるヒヤリハット事例・対策集」を見てみる
目次
倉庫・物流作業における事故件数と危険性
まずは倉庫・物流作業で実際に発生した事故件数の推移を見てみましょう。
中央労働災害防止協会が公表している資料をもとに、2018年から2023年までの倉庫業における事故件数を下表にまとめました。
年度 | 事故件数 |
---|---|
平成30年(2018年) | 615件 |
令和元年(2019年) | 666件 |
令和2年(2020年) | 685件 |
令和3年(2021年) | 781件 |
令和4年(2022年) | 821件 |
令和5年(2023年) | 863件 |
参照元:労働災害分析データ 倉庫業(PDF)|中央労働災害防止協会
このデータは倉庫業の事故件数が年々増えていることを示しており、事故につながりかけた危険な事象「ヒヤリハット」も増加傾向にあると推測できます。
一般的に倉庫や物流の現場は繰り返しの単純作業が多く、仕事に慣れた作業員ほど注意を怠りがちになることがヒヤリハットの一因と考えられます。加えて、短時間労働者が多い現場では安全教育が十分に行き届かず、倉庫・物流作業における基本的なルールやリスクへの意識が浸透しにくいという課題もあります。
物流業や倉庫業に限らず、現場業務における労働災害の対策は喫緊の課題としてあらゆる現場で取り上げられています。以下の記事では、倉庫作業における具体的な安全対策や事故の防止を実現している企業事例を紹介してるのであわせてご覧ください。
関連記事:倉庫作業の安全対策12選:事故防止を実現する物流企業事例も紹介
【作業別】倉庫・物流作業のヒヤリハット事例集
1件の重大事故には29件の軽傷事故と300件の無傷事故があるという「ハインリッヒの法則」が示すように、事故の裏には数多くの「危険」が存在しています。具体的にどのような危険が起こり得るのか、ここからは倉庫・物流作業におけるヒヤリハットの事例を作業別に紹介します。
- フォークリフト作業でのヒヤリハット事例
- 手荷役作業でのヒヤリハット事例
- ピッキング作業でのヒヤリハット事例
- 検品作業・梱包作業でのヒヤリハット事例
- トラック運転中やトラックヤードでのヒヤリハット事例
これから紹介するヒヤリハット事例は多岐にわたりますが、それらのヒヤリハット事例を踏まえてどのように労災や事故を未然防止するべきなのかなどの対策については、「ヒヤリハット事例を活かした事故やトラブルの防ぎ方は?危険を伝えるマニュアル作りも解説」の記事で別途解説しているのでご覧ください。
また、現場で発生したヒヤリハットをイラストを交えて解説している資料も用意しています。
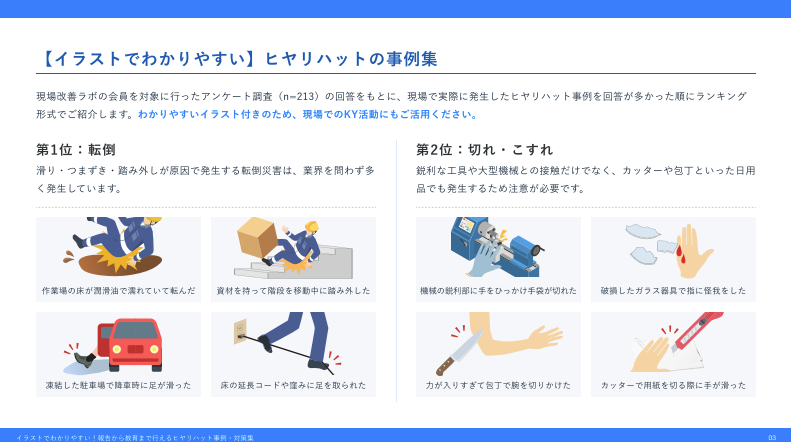
【イラストでわかりやすい!報告から教育まで行えるヒヤリハット事例・対策集】より抜粋
本資料では、現場改善ラボの会員に対して行ったヒヤリハットの調査(n=213)を基にして作成しており、現場の実態に即した内容となっています。再発防止対策や企業事例も掲載しているので、物流現場のヒヤリハットを対策する上でのヒントも得られるはずです。以下のリンクをクリックしてぜひご覧ください。
>>「イラストでわかりやすい!報告から教育まで行えるヒヤリハット事例・対策集」を見てみる
フォークリフト作業でのヒヤリハット事例
フォークリフト作業では操作ミスや不注意によるヒヤリハットが起きやすく、小さな危険が重大な事故につながる恐れがあります。ここではフォークリフト作業におけるヒヤリハット事例を紹介します。
バック走行中に作業員と接触しそうになった
【ヒヤリハットの詳細】
ある倉庫でフォークリフトを運転していた作業員は、バックをする際にフォークリフトの後方が死角になったことで作業員に気づかず、もう少しで衝突しそうになった。幸いにも、後方の作業員がすぐに気づいて避けたため、事故には至らなかった。
原因 | ・バック走行中に周囲の確認を怠っていたこと ・フォークリフトの後ろ側は死角が多く、歩行者に気付けなかったこと |
ヒヤリハット対策 | ・フォークリフトを運転する際は周囲を確認し、必ず安全性を認識してから走行させる ・フォークリフトが作業員の通路を横断しない動線を確保する |
ブレーキがすぐに効かずぶつかりそうになった
【ヒヤリハットの詳細】
作業員がリーチ式のフォークリフトに乗ったところ、ブレーキの効きが非常に遅く、思い通りに停止できなかった。これにより、物に接触しそうになったり、人にぶつかりそうになったりと、危険な場面が発生した。
原因 | ブレーキの効きが想定以上に遅かったこと |
ヒヤリハット対策 | ・早めのブレーキ操作を意識する ・走行経路や動線を見直し、他の作業員と接触しにくいルートを設計する |
天井に接触しそうになった
【ヒヤリハットの詳細】
段積みしたパレットから2段目の荷物を降ろす際、フォークリフトのマストが天井に接触しそうになって危険を感じた。
原因 | ・物流センターの天井が低かったこと ・フォークリフトを使用する前提で作られていなかったこと |
ヒヤリハット対策 | ・天井が低い物流センターでは接触の危険性があることを認識する ・荷物を高く持ち上げないようにする ・フォークリフトで操作可能な高さに合わせて「高さ制限ライン」を設置する |
フォークリフト作業のヒヤリハット事例と実践的な安全対策は、以下の記事でより詳しくまとめられています。本記事とあわせて参考にしてください。
▼関連記事▼
・フォークリフトのヒヤリハット事例集と対策まとめ!危険予知の事例もあわせて解説
・フォークリフトの安全対策8例!事故を防止した改善事例や安全意識を高める方法も解説
手荷役作業でのヒヤリハット事例
フォークリフトを使わず、人の手で荷物を持ち上げたり積み降ろしたりする作業を「手荷役作業」といいます。ここでは手荷役作業におけるヒヤリハット事例を紹介します。
高所から商品が落下して接触しそうになった
【ヒヤリハットの詳細】
作業員の身長より高い位置にある棚から商品Aを取ろうとしたところ、持ち上げた商品Aを隣に置いていた商品Bに当ててしまった。脚立を取りに行くのが面倒だったこと、手を伸ばせばなんとか届く位置にあったことから、脚立を使わなかった。商品Bは落下したが、幸いにも作業員に接触することはなく、怪我には至らなかった。
原因 | ・脚立を使わずに高所作業を行ったこと ・無理に手を伸ばしてしまったこと |
ヒヤリハット対策 | ・高所作業を行うときは必ず脚立を使用する ・高い位置にある棚には軽い商品を優先して配置する |
トラックの荷台から転落しそうになった
【ヒヤリハットの詳細】
トラックの荷台に乗り、積載していた荷物を降ろそうとしたところ、足元が滑って体のバランスを崩した。荷台から転落しそうになったが、間一髪でなんとか持ち堪えた。
原因 | ・荷台の床面が濡れて滑りやすい状態だったこと ・すぐに次の作業に取り掛からなければならず、焦りがあったこと |
ヒヤリハット対策 | ・滑り止め対策として荷台マットを活用する ・作業に配分しているリソースを見直し、十分な作業時間と人員を確保する |
長時間の作業で握力が弱まり荷物を落としそうになった
【ヒヤリハットの詳細】
作業員の欠勤があり、通常より少ない人数で作業をすることになった。休憩をほとんど取らずに荷物の積み込みをしていたところ、だんだん手に力が入らなくなり、荷物を落としそうになった。
原因 | ・長時間の作業により疲労が蓄積していたこと ・握力が落ちている自覚はあったが、そのまま作業を続けてしまったこと |
ヒヤリハット対策 | ・休憩時間の確保を徹底する ・重要度の高い作業を優先し、少人数のときは一時的に作業量を減らすことも検討する ・滑り止め手袋を着用して安全性を高める |
ピッキング作業でのヒヤリハット事例
倉庫内を移動しながら商品を集めるピッキング作業は、ヒヤリハットが起きやすい作業の1つです。ここではピッキング作業におけるヒヤリハット事例を紹介します。
脚立のバランスが崩れて高所から転落しそうになった
【ヒヤリハットの詳細】
棚の一番上に置いている商品を取るために脚立を使用したが、天板に乗ったときにバランスが崩れてしまい、高所から転落しそうになった。作業員が小柄だったため、天板に乗らなければ商品まで手が届かなかった。
原因 | ・脚立の天板に乗ったこと ・作業員の身長が低く、踏ざんに乗っても商品まで手が届かなかったこと |
ヒヤリハット対策 | ・脚立を使用する際は天板に乗らないようにする ・高所作業時にはヘルメットや安全帯を使用する ・手すり付き脚立を導入する ・高所作業は他の作業員に変わってもらう(無理をしない) |
台車を引きながら移動しているときに他の作業員と接触しそうになった
【ヒヤリハットの詳細】
商品をピッキングするために台車を引いていたところ、曲がり角で他の作業員とぶつかりそうになった。台車に商品を積み重ねており、進行方向が見えづらい状態だった。
原因 | ・台車に商品を積み過ぎて視界が塞がっていたこと ・曲がり角が死角となり、他の作業員の存在を認識できなかったこと ・走行ルートの通路が狭く、台車を移動させづらかったこと |
ヒヤリハット対策 | ・台車には適切な量の商品を積み、視界を塞がないようにする ・曲がり角を通るときは一旦立ち止まって安全確認をする ・台車の走行ルートの通路を広くする(倉庫内の動線を見直す) |
重い商品を持ち上げるときに転倒しそうになった
【ヒヤリハットの詳細】
床に置いている商品を台車に乗せようとし、立位のまま腰を曲げて商品を持ち上げたところ、腰に過度な負荷がかかって後ろに倒れそうになった。数日前から取り扱いを開始した新しい商品であり、作業員が想像していたよりも重量のある商品だった。
原因 | ・ブレーキ無理な姿勢で商品を持ち上げようとしたこと ・商品の重量を確認していなかったこと |
ヒヤリハット対策 | ・重い商品を持ち上げるときは膝を曲げて重心を低くする ・見慣れない商品を扱うときは事前に重量を確認する ・無理に商品を持ち上げようとしない |
ここではピッキング作業におけるヒヤリハット事例を紹介しましたが、同じように、ピッキングミスの改善にも課題を感じている現場は多いと思います。以下の記事では、ピッキングミスの改善手法や事例について解説されているので、あわせて参考にしてみてください。
▼関連記事▼
・ピッキングミスや数量間違いが多い人の特徴と9つの対策!改善事例もあわせて紹介
・ピッキング改善事例5選:生産性向上や効率化を実現するポイントとは?
検品作業・梱包作業でのヒヤリハット事例
商品の検品や梱包は細かい作業が多く、長時間の作業で集中力が低下したときにミスが起こりやすくなります。ここでは検品作業・梱包作業におけるヒヤリハット事例を紹介します。
カッターナイフで指を切りそうになった
【ヒヤリハットの詳細】
商品の入荷検品で外装のダンボール箱を開けるとき、片手で箱を押さえながらカッターナイフを使ったところ、刃が勢いよく滑って指の方に向かってきた。
検品時にカッターナイフを使うときは軍手を着用するルールだったが、作業台に置いていたはずの軍手が見つからず、このときは素手で作業してしまった。怪我には至らなかったものの、もう少しで指を切るところだった。
原因 | ・ダンボール箱を押さえる手を刃の進む方向に置いていたこと ・作業中に軍手を着用していなかったこと ・安全性の低い一般的なカッターナイフを使用していたこと |
ヒヤリハット対策 | ・刃の進行方向に手を置かない ・カッターナイフを使うときは軍手を着用する ・刃が自動的に戻るセーフティカッターを使用する |
複数の商品を同時に検品していて内容を取り違えそうになった
【ヒヤリハットの詳細】
商品の出荷検品は出荷指示書やピッキングリストに従って目視で確認している。複数の指示書を作業台に並べて作業していたところ、別の商品と照らし合わせて検品を進めそうになった。途中で品番の違いに気付き、梱包前に検品をやり直すことができたが、気付かずに進めていれば誤出荷につながる可能性があった。
原因 | ・狭い作業スペースで複数商品の検品作業を行っていたこと ・指示書と品番の突き合わせを行わず、商品の外観だけで判断していたこと |
ヒヤリハット対策 | ・広い作業スペースを確保し、未検品・検品中・検品済みで区画を分ける ・ハンディターミナルによるバーコード照合の導入など、検品作業を目視からツールへ切り替える |
床に落ちていた緩衝材で足を滑らせそうになった
【ヒヤリハットの詳細】
梱包作業で使用する緩衝材が床に散乱しており、足を取られて滑りそうになった。緩衝材は大きなダンボール箱にまとめて保管しているが、作業のたびに出し入れするのが煩わしく、一度に大量の緩衝材を取ってきて作業台の周囲に置きっぱなしにしていた。
原因 | ・床に落ちた緩衝材を拾わずに放置していたこと ・保管箱からあふれるほどの大量の緩衝材を入れていたこと ・緩衝材の保管箱が1つしかなく、作業エリアによっては取りに行く必要があったこと |
ヒヤリハット対策 | ・作業開始前に緩衝材や障害物が落ちていないか確認する ・梱包作業が終わったら速やかに片付けるルールを徹底する ・緩衝材は保管箱に入る量だけ保管する ・緩衝材の保管箱を増やし、各作業エリアの近くに設置する |
トラック運転中やトラックヤードでのヒヤリハット事例
トラックの運転やトラックヤードでの作業は、一歩間違えると重大な事故につながる可能性が高く、常に慎重な対応が求められます。ここではトラック運転中やトラックヤードにおけるヒヤリハット事例を紹介します。
路面凍結によってスリップ事故が起きそうになった
【ヒヤリハットの詳細】
ある冬の朝にトラックを運転していたところ、ブレーキをかけた瞬間にタイヤがスリップした。車両が横滑りして反対車線にはみ出してしまったが、幸いにも対向車は来ておらず、事故には至らなかった。
原因 | ・路面凍結によって道路が滑りやすくなっていたこと ・ブレーキをかける力が強かったこと |
ヒヤリハット対策 | ・事前に天気予報と道路状況を確認し、場合によっては出発を遅らせる ・凍結した道路を走るときはスピードを落とし、ゆっくりとブレーキを踏むようにする |
ブレーキをかけたときに荷崩れを起こしかけた
【ヒヤリハットの詳細】
トラックの運転中、前方の脇道から車が飛び出してきて急ブレーキをかけた。そのときに積荷のバランスが崩れ、荷崩れが起こりそうになった。すぐにトラックを安全な場所に停めて積荷の固定をやり直し、危険な状況を回避できたものの、重大な事故につながりかねない状況だった。
原因 | ・積荷の際に荷物がしっかりと固定されていなかったこと ・荷台の片側に重量が偏っており、急ブレーキ時に荷崩れが起こりやすい状態にあったこと |
ヒヤリハット対策 | ・ロープや固定具を使用して荷物をしっかりと固定する ・荷物のバランスを考慮し、前後左右に偏りが出ないように積み込む ・予期せぬ事態に備えて、前方車両との車間距離を広く取る |
雨天時にトラックヤードの床が濡れて滑りそうになった
【ヒヤリハットの詳細】
雨天時にトラックヤードで荷物の積み降ろしを行っていた際、強い風で雨がヤード内に吹き込み、床が濡れて滑りやすくなっていた。作業員がその上を歩行したところ、足を滑らせそうになり、体のバランスを崩した。
原因 | ・雨によってヤードの床が濡れていたこと ・濡れた床の状態に気付いていたが、特に注意せずにその上を歩いたこと ・ヤードの床に滑り止め対策をしていなかったこと |
ヒヤリハット対策 | ・雨天時はヤードの床が滑りやすくなることを周知し、慎重な歩行を促す ・耐滑性のある安全靴を着用する ・ヤードの床に滑り止めシートを敷く |
労災ゼロを目指すためのヒヤリハット防止対策
倉庫・物流作業には多くの危険が潜んでおり、常に慎重な作業が求められます。
小さなヒヤリハットを見逃すと、注意すべきサインに気付けないまま作業を続けてしまい、それが重大な労働災害につながる恐れもあります。こうしたリスクを回避するためには、倉庫内で起きたヒヤリハットの原因を明らかにし、再発防止に努めることが重要です。
倉庫作業で労災ゼロを目指すためには以下のような安全対策が必要です。
- 作業標準化がなされる仕組み作り
- 安全教育のためのマニュアルや手順書整備
- 危険予知(KY)活動の実施
- ヒヤリハット事例や報告書の共有
- 外国人労働者やパートタイム作業員の教育体制整備
- 5S活動の実施
- 指差呼称や声かけのルール化
- 作業動線の見直し
- 安全設備の導入
- 保護具の導入
それぞれの具体的なやり方や詳細な解説は、関連記事「倉庫作業の安全対策12選:事故防止を実現する物流企業事例も紹介」で詳しくまとめられています。倉庫作業の安全対策を推進したい場合は、あわせて参考にしてみてください。
また、以下の資料では、現場作業に従事する方(213名)を対象に行ったヒヤリハットの調査レポートをもとに、ヒヤリハットの対策・再発防止策を解説しています。ヒヤリハットの発生原因から具体的な対策まで体系的に学べる資料ですので、社内に展開して早急な対策を講じることができます。以下の画像をクリックし、資料をダウンロードしてみてください。
>>「イラストでわかりやすい!報告から教育まで行えるヒヤリハット事例・対策集」を見てみる
倉庫作業ヒヤリハットの「見える化」で労災を防止する企業事例
ここからは、倉庫作業の安全意識を高め労災を防ぐための取り組み例として、物流企業の取り組み事例を紹介します。これから紹介する企業や現場はいずれも、ヒヤリハットや危険な作業を「映像」や「動画」におさめ、従業員の安全教育を実施しています。
カゴ台車のヒヤリハット見える化と安全周知
ある総合物流会社では、安全対策を一方通行で教育するのではなく、「なぜ実施しなければならないのか?」「安全対策を怠ることで具体的にどのような災害が起きるのか?」を動画で教育しています。
例えば以下の動画マニュアルは、同社が実際に撮影した、カゴ台車の落下事故の様子です。キャスターロックをかけないことでどのような災害が起きるのか、字幕も取り入れながら一目でわかるようになっています。
▼カゴ台車のヒヤリハット動画と安全周知▼
※「tebiki」で作成
こうした安全教育を実施しつつ、カゴ台車の適切な扱い方について動画マニュアル化もしており、従業員の安全意識向上や標準化に努めています。
▼カゴ台車のキャスターロック方法を解説した動画マニュアル▼
※「tebiki」で作成
何が危険で何が安全か、一目でわかるような教育体制・マニュアル整備は、現場の安全性を向上させる1つの有効手段と言えます。その意味で上記のような動画マニュアルは安全対策に優れており、多くの物流現場で活用されています。
フォークリフトの禁止操作を映像で教育
物流企業「株式会社近鉄コスモス」は、フォークリフトの禁止事項やNG操作を動画におさめ、動画マニュアルとして展開することで、安全意識の向上に努めています。以下は実際に同社で活用されている動画マニュアルです。
▼安全意識の向上につながる動画マニュアルの例▼
※「tebiki」で作成
「動画」と聞くと「撮影の手間がかかりそう」「編集が大変で、紙の手順書より時間がかかりそう」と思われるかもしれませんが、現場従業員でも気軽に作れる動画マニュアルであれば、効率的なマニュアル整備と教育が可能です。
事実として、ここまで紹介した上記の動画はすべて現場従業員によって撮影・編集・公開されています。すべて現場作業に特化した動画マニュアル作成ツール「tebiki現場教育」で作られており、特別な技術や機材は一切不要です。tebikiの詳細な機能や活用事例が気になる方は「3分で分かる『tebikiサービス資料』」をご覧ください。
下の画像をクリックすると、資料ダウンロードができます。
物流現場における動画マニュアルの具体的な活用方法や導入効果について、さらに詳しくまとめた資料をご用意しています。自社の課題解決のヒントとしてご活用ください。
>>>「物流業界の生産性向上を助ける動画マニュアルのチカラ(pdf)」を見てみる
実際にどのような動画マニュアルが業務で使われているのか、具体的なサンプルを見てみたい方は、以下の資料が役立ちます。様々な現場の動画サンプルがまとめられており、自社での活用イメージを膨らませるのに最適です。
>>>「実際に業務で使われている動画マニュアルのサンプル集(pdf)」を見てみる
まとめ:倉庫の安全は「ヒヤリハットの可視化」から
本記事では、倉庫・物流現場に潜む様々なヒヤリハット事例とその対策について、作業別に解説してきました。フォークリフト作業の危険性から、手荷役、ピッキング、検品・梱包、トラック輸送に至るまで、日常業務には多くのリスクが伴います。
ハインリッヒの法則が示すように、重大な事故を防ぐためには、これらの「ヒヤリ」とした経験を決して軽視せず、原因を分析し具体的な再発防止策を講じることが不可欠です。その上で、安全な作業手順を確立し、全ての作業員にその内容を確実に浸透させるための「安全教育」が極めて重要となります。
特に、本記事の企業事例でも紹介したように、「動画マニュアル」を活用した安全教育や安全対策は非常に有効な手段です。動画は、文字や口頭説明だけでは伝わりにくい実際の危険な状況や正しい動作、作業のコツ・カンを視覚的に、かつ分かりやすく伝えることができます。
現場作業に特化した動画マニュアル作成ツール(例:tebiki現場教育)であれば、従業員の稼働時間を圧迫することなく、現場のマニュアル整備が可能になります。物流現場における動画マニュアルの可能性や活用イメージについては、以下のリンクから資料をご覧いただけます。ぜひ参考にしてみてください。