かんたんデジタル現場帳票「tebiki現場分析」を展開する現場改善ラボ編集部です。
生産設備の安定稼働を維持するためには、適切な保全が欠かせません。しかし、「設備の故障による生産停止を防ぎたい」「修理コストを抑えたい」と考える現場担当者の多くが、従来の時間基準保全(TBM)頼みになっているケースもよく耳にします。
そこで注目されているのが、状態基準保全(CBM)です。本記事では、「状態基準保全とは何か?」という基本から、他の保全方式との違い、導入に際しての課題まで詳しく解説します。
目次
状態基準保全(CBM)とは?他の保全との違いも解説
設備の安定稼働を維持し、ムダな修理コストを抑えるためには、適切な保全方式の選択が重要です。その中でも、リアルタイムで設備の状態を監視し、必要に応じて最適なメンテナンスを行う「状態基準保全(Condition-Based Maintenance)」が注目されています。
ここでは、以下の観点から状態基準保全(CBM)について詳しく解説します。
- 状態基準保全(CBM)の定義
- 状態基準保全(CBM)で使われる技術
- 状態基準保全(CBM)と他の保全方式との違い
状態基準保全(CBM)の定義
状態基準保全(CBM)とは、設備の状態をリアルタイムで監視し、異常が検知されたときに必要なメンテナンスを行う保全方法です。適切な保全による設備の稼働率向上や、ムダな保全の削減によるコストダウンが期待できます。
従来の時間基準保全(TBM:Time-Based Maintenance)では、一定の期間ごとに定期点検や交換作業を行うため、故障していない部品の無駄な交換が発生することがありました。一方、CBMでは実際の設備の状態に基づいて保全作業を実施するため、無駄な交換や点検を減らしつつ、故障のリスクを抑えることが可能です。
例えば、振動や温度、電流などの状態データをセンサーで取得し、異常が検知されたタイミングで適切な対応を行うことで、設備の寿命を最大限に活かせます。
状態基準保全(CBM)で使われる技術
状態基準保全(CBM)の実現には、デジタル技術を活用したモニタリングや検知が欠かせません。主に使用されることの多い技術例は以下の通りです。
技術 | 詳細 |
---|---|
デジタル帳票 | 点検や異常情報の記録をデジタル化し、 情報の共有・蓄積・分析を効率化 |
IoT | 設備の状態をデータとしてリアルタイムに収集 |
AI | 収集したデータを分析し、 異常パターンの検出や故障予知を実施 |
センサー技術 | 設備の状態を細かく監視し、 異常発生時に即座にアラートを発信 |
データ分析 | 設備の劣化状況の把握や、故障予兆の検知 |
リアルタイム 監視システム | 設備の状態を常時監視し、異常発生時に迅速に対応 |
上記のうち、「記録情報の見える化とデータ活用を促進できる」 という理由からCBMを推進するうえで特に推奨されるのが「デジタル帳票」です。代表例として「tebiki現場分析」のようなツールが挙げられますが、デジタル帳票に関する理解は以下の資料で深められます。
>>デジタル帳票とはどんなツール?記録・承認・集計の悩みを解決できる理由を詳しくみる(無料配布中)
状態基準保全(CBM)と他の保全方式との違い
状態基準保全(CBM)と比較されることの多い保全について、それぞれの違いを表形式でまとめました。主に、保全のタイミングや目的に大きな違いが見られるため、整理すると良いでしょう。
定義 | 保全のタイミング | 目的 | |
---|---|---|---|
状態基準保全 (CBM) | 設備の状態をリアルタイムで監視し、異常の兆候に基づき実施される保全 | センサーやIoTで収集したデータから異常を検知した時 | 故障が発生する前に対策し、ダウンタイムを最小化 |
時間基準保全 (TBM) | 一定の稼働時間や期間ごとに定期的に行われる保全 | 事前に決めた稼働時間や期間(例:1,000時間ごと) | 計画的なメンテナンスで突発的な故障リスクを低減 |
予防保全 (PM) | 過去の故障データや経験則に基づき、故障を未然に防ぐための保全 | 故障履歴に基づき設定された周期(例:3年ごとに交換) | 過去の事例を活用し、故障の発生頻度を低減 |
事後保全 (BDM) | 設備が故障してから修理・交換を行う保全 | 故障発生後に対応 | 初期コストを抑え、必要な場合のみ対応 |
また、それぞれのメリットとデメリットを簡単にまとめると、以下の通りです。
状態基準保全 (CBM) | 必要時のみ保全を行うためムダなメンテナンスを削減できるが、 センサー導入などの初期投資が必要 |
時間基準保全 (TBM) | 保全計画が立てやすいが、 過度なメンテナンスでムダが発生しやすい |
予防保全 (PM) | 故障を未然に防ぎやすいが、 設備ごとの個別対応やデータの蓄積が難しい |
事後保全 (BDM) | 故障時のみ対応するためローコストだが、 突然の故障や生産停止のリスクがある |
それぞれの保全について、「トラブルに対応するうえで自社に最も適しているのは何か?」という軸をもとに最適なものを選びましょう。
今回ご紹介した保全方法についてより詳しく知りたい方は、以下の記事もご覧ください。
関連記事:予防保全・予知保全・事後保全は何が違う?メリットデメリット、事故を防ぐポイント
状態基準保全(CBM)が注目されている背景やメリット
製造現場では、設備の老朽化や生産形態の多様化により、設備トラブルによる生産停止や品質不良のリスクが高まっています。しかし、従来の事後保全(BDM)では故障が発生してから対応するため、生産ラインが長時間停止したり、多大な修理コストや部品交換費用が発生する課題があります。さらに、予測できないトラブルによる納期遅延や顧客への影響も避けられません。
こうした背景から、IoTやAI技術を活用し、設備の状態をリアルタイムに把握・分析できる「状態基準保全(CBM)」が注目されています。以下に、CBM導入のメリットを表形式で解説します。
突発停止の防止 | リアルタイム監視で故障の前兆を早期検知し、 予期せぬ停止(チョコ停・ドカ停)を防止。 |
保全コストの最適化 | 必要な時だけ保全を行い、 不要な部品交換や作業を減らしてコスト削減。 |
設備稼働率・生産性の 向上 | 停止時間を減らし稼働率を高め、 安定した生産と納期遵守を実現。 |
品質リスクの低減 | 異常発生前に対処し、 不良品や品質トラブルのリスクを抑制。 |
データ活用による 保全精度向上 | IoT・AI分析で保全判断の精度を上げ、 設備改善にも活用可能。 |
設備寿命の延長 | 過剰保全を避けつつ早期対応で設備劣化を防ぎ、 寿命を延ばす。 |
これらのメリットが得られるCBMは、設備保全DXの第一歩だといえます。設備の異常を早期に捉え、ドカ停を未然に防ぐ設備DXの具体的な進め方や予防保全 / 予知保全へのつなげ方について知りたい方は、以下のリンクをクリックし詳細なハンドブックをご覧ください。
>>設備トラブルによる生産性低下を解消!設備保全DXを叶える具体的な取り組みをみる(無料配布中)
状態基準保全(CBM)の導入5ステップ
効果的な導入には、設備の選定からメンテナンス計画の策定・評価まで、適切なステップに沿って行うことが重要です。以下の5つのステップを踏むことで、設備の稼働率向上と保全コストの最適化を実現できます。
対象設備の選定
状態基準保全(CBM)の導入にあたり、まずどの設備に適用するのかを選定することが大切です。工場内の全ての設備にCBMを導入するのは現実的ではないため、異常が発生しやすい機器や生産ラインのボトルネックとなる設備を優先的に選ぶ必要があります。
例えば、高価で交換が難しい設備や、生産プロセスにおいて重要な役割を果たす機械はCBM導入の優先候補です。これらの設備を選定することで、故障による生産停止のリスクを最小限に抑えられます。
センサーの設置
次に、選定した設備の状態を把握するためにセンサーを設置します。センサーの種類は、設備の劣化を示す指標に基づいて決定します。具体的には以下のような種類が挙げられます。
- 温度センサー:設備の過熱を検知
- 振動センサー:異常振動による故障の兆候を把握
- 音センサー:異音による異常を検出
- 電流センサー:電流値の変化から異常を特定
これらのセンサーを適切に設置し、リアルタイムで設備の状態を監視できる環境を整えることがCBMの基本となります。
また、センサーによるリアルタイム監視に加えて、日常点検や作業記録をデジタル現場帳票で蓄積・分析することでも設備状態の把握や異常傾向の検出は可能です。
例えば、点検時の温度や圧力、作業時の異常発生記録などをデジタル化し過去データと比較・集計することで、センサーでは捉えきれない異常の兆候や保全タイミングを見極めることができます。センサーとデジタル帳票を併用することで、より精度の高い状態基準保全が実現できます。
デジタル帳票とは何か?や、どのように記録していくか、導入効果について詳しく知りたい方は以下のハンドブックをご覧ください。
>>デジタル帳票とはどんなツール?記録・承認・集計の悩みを解決できる理由を詳しくみる(無料配布中)
データ収集
センサー設置後は、設備の運転状態や異常に関するデータをリアルタイムで継続的に収集します。このデータ収集の主な目的は、設備が正常に稼働している際の動作パターンを詳細に把握し、正常時と異常時の挙動の違いを明確にすることにあります。
近年では、収集したデータをAIや機械学習による分析に活用するケースも増えています。具体的には、過去のデータから故障に先行する特徴的なパターンをAIが学習し、そのパターンが現れた際に早期に異常を検知できるよう精度を高めます。これにより故障予測の信頼性が向上し、適切なタイミングでの保全が可能となります。
分析
収集したデータを基に、設備の劣化状況や異常の発生するパターンを分析します。データを長期的に蓄積することで故障の前兆となる要因を特定し、予測が可能です。
分析の手法としては、以下のようなものがあります。
方法 | 詳細 |
---|---|
トレンド分析 | 過去のデータと比較し、設備の劣化スピードを測定 |
異常検知アルゴリズム | 正常な動作パターンから逸脱した動きを検知 |
統計モデルによる予測 | 異常の発生確率を算出し、事前対策を立案 |
この分析を基に、適切なタイミングでのメンテナンスが可能となり、突然の故障リスクを低減させます。
現場で集めたデータを分析するにあたり、まずは改善につながる「正しい」データ活用の基盤を整える必要があります。「データが集まらない」「分析結果活用のイメージが持てない」とお悩みの方は、本記事の他以下の画像をクリックし専門家による解説動画をご覧ください。
保全計画の策定、実施、評価
最後に、計画の策定と実施・評価を行います。計画を立てる際には、以下の点を考慮する必要があります。
- どのタイミングで点検・メンテナンスを行うか
- どの部品を優先的に交換するか
- 異常発生時の対応フローを明確にする
CBMの導入によって、設備の故障率やメンテナンスコストがどの程度削減されたのかを測定し、必要に応じて計画の見直しを行います。
プロセスを適切に進めることで、設備の稼働率向上やメンテナンスコストの最適化、突発的な故障の予防を実現できます。導入する際には、これらのステップを参考にしながら、計画的に進めていくことが重要です。
状態基準保全(CBM)の事例3選
実際にCBMを活用し、設備管理の改善を進めている企業の事例を3つご紹介します。
- 共栄工業株式会社
- 旭化成エンジニアリング
- JR東日本
共栄工業株式会社
スチール製家具の生産・販売を行う共栄工業株式会社では、デジタル帳票による保全記録の見える化を通じて状態基準保全を実践しています。従来は紙帳票を使い、設備の点検結果や温度・薬品濃度など重要な管理項目を記録していましたが、転記作業やデータ集計に時間と手間がかかり、記録を活かした改善活動まで手が回らないという課題を抱えていました。
そこで同社では、デジタル帳票(tebiki現場分析)を活用し保全記録をデジタル帳票で一元管理。現場で直接入力したデータがリアルタイムで集計・可視化されることで、設備の異常傾向や作業状況をすぐに把握できるようになりました。その結果、従来1日2時間かかっていた記録の集計作業が約1分に短縮され、設備トラブルの予兆管理や品質改善のための分析もスムーズに実施可能に。
保全記録をただ蓄積するだけでなく、現場の状態変化を即時に把握し、設備や工程の最適なタイミングでメンテナンスや改善を行うという状態基準保全の仕組みを、デジタル帳票の導入によって実現しています。
同社によるデータ活用の様子や「導入して良かった」と感じるおすすめポイントについては、以下のインタビュー記事内で詳しくご紹介しています。
インタビュー記事:1日2時間の集計作業が約1分に。スチール製家具製造の共栄工業のデジタル改革
旭化成エンジニアリング
旭化成エンジニアリングでは、長年にわたる設備管理の経験とノウハウを活かし、計画保全システムを導入しています。このシステムでは、設備の状態を詳細に評価し、適切なメンテナンス計画を立案することで、保全業務の効率化とコスト削減を実現しています。
同社ではまず、現状の保全水準を評価し、設備の「あるべき姿」を設定することからスタートしています。このプロセスにより、無駄な保全作業を減らし、設備の寿命を最大限に引き延ばすことが可能になりました。
次に、計画保全の体制を構築し、「TMQ®(Total Maintenance Quality)」と呼ばれる独自の保全支援ツールを活用しました。これにより、設備の状態を正確に把握し、故障の予兆を検知できます。さらに、設備診断機器を活用してCBMを推進し、故障修理件数の削減を実現しました。
この取り組みによって、旭化成エンジニアリングは生産の安定性を向上させ、設備のダウンタイムを最小限に抑えることに成功しています。また、計画保全とCBMを組み合わせることで、長期的なコスト削減にもつながっています。
参照:計画保全事例|設備診断|旭化成エンジニアリングのオンライン展示会 CONNECT
JR東日本
鉄道業界においても、設備の適切な保守・点検は、安全で安定した運行を支える重要な要素です。JR東日本では、これまで時間基準保全(TBM)を基本とし、定期的な点検やメンテナンスを実施してきました。しかし、さらなる安全性の向上とメンテナンス業務の効率化を目指し、CBMの導入を進めています。
CBMの導入により、鉄道設備のトラブルや事故の予兆を把握し、設備故障が発生する前に適切なメンテナンスを実施できるようになりました。これにより、突発的な設備故障による運行遅延や重大事故のリスクを大幅に低減できます。
また、センシング技術やICT(情報通信技術)を活用し、設備の状態をリアルタイムで監視することで、最適なタイミングでの保全作業が可能になりました。例えば、鉄道車両のモーターや車軸の振動・温度を監視することで、異常の兆候をいち早く検知し、適切な対応をとれます。
この取り組みによって、JR東日本は「究極の安全」の実現とメンテナンス部門の生産性向上を同時に達成することを目指しています。今後も、さらなるCBMの活用により、より効率的な鉄道保守システムの構築が期待されます。
参照:メンテナンス × CBM ~先端技術を活用した技術革新の取組み
【導入前に確認】状態基準保全(CBM)を導入してもうまくいかない現場の共通点
状態基準保全(CBM)は「データで設備の状態を判断し、ムダな点検や突然の故障を減らす」ための手法です。ですが、実際に現場で導入しても思うように成果が出ないケースが後を絶ちません。そんな現場に共通するのが、次のような“見えない課題”です。
“見て終わり”のデータが溜まるだけで分析につながらない
状態基準保全(CBM)導入の第一歩として、振動や温度、圧力といった設備データを収集できる環境を整える企業は増えています。しかし実際には、データが蓄積されるだけで活用されず、単なる“記録”にとどまっているケースが多く見受けられます。
例として、「グラフは見てるけど、異常値が出たときだけ反応すればいいと思っている」「データは蓄積しているが、後から振り返ることはない」といった声が現場から上がることも珍しくありません。
しかし、故障は突然やってくるもの。普段からデータの動きを追い、傾向を掴んでおかないと、結局「壊れてから対応」になってしまいます。
こうした状況では、設備の異常兆候を早期に発見し、故障リスクを低減するという状態基準保全(CBM)本来の目的を果たすことは困難です。
紙の帳票では情報が埋もれて探せない
紙帳票による記録は記入内容の統一や検索性に課題が残り、せっかくの点検情報が埋もれてしまうリスクがあります。特に、設備台数が多い工場や複数拠点を持つ企業ほど、この課題は顕著になります。
また、人によって記録の書き方がバラバラで「字が読めない」「温度なのか圧力なのかよく分からない」など、記録の質にもバラつきが出やすいのも問題です。このような状況では、記録自体が“その場限り”のデータになり、不調や異常の兆候を掴むことが困難だといえるでしょう。
実際に、株式会社日本電気化学工業所では「過去データの参照や傾向分析を行う際も、膨大な紙の記録から必要な情報を抽出するのに、相当な労力がかかる」という課題を抱えていました。
同社がこの課題を解決できた理由については、後述する事例紹介で詳しく解説しています。
Excelでは分析の工数が大きく現場の負担に
紙帳票を避けExcelでデータ管理している場合でも、実は落とし穴になりがちです。例えば、現場で収集したデータをExcelへ転記し、グラフ化や集計を手作業で行う場合、その工数は決して小さくありません。
加えて、特定の担当者だけがExcelの扱い方や集計方法を把握しており、属人的な管理になってしまっているケースも少なくありません。データをまとめる人が限られ、さらに本来の業務の合間を縫って対応しているため毎月の分析レポートを作るだけで疲弊するなど、状態基準保全(CBM)の運用が「データ管理の仕事」を増やす結果になりかねないでしょう。
設備保全担当者にとって本来の業務は点検や整備であり、データ入力や加工に膨大な時間を取られることは本末転倒です。せっかく集めたデータも「まとめるだけで終わり」「報告書を作ることが目的化してしまう」といった形骸化が進み、設備の故障予防や改善につながらないまま埋もれてしまうことにもつながりかねません。
点検結果の判断が結局ベテランの“カンコツ”任せ
状態基準保全(CBM)導入の目的はデータに基づく客観的な判断を行うことですが、実際の現場では依然としてベテラン社員の経験や勘に頼る場面が多く残ります。モニタリングや点検の仕組みは整えていても、最終的な判断は「長年の経験があるあの人に頼りきり」という現場も珍しくありません。
しかし、ベテランならではのカン・コツといった感覚的な判断は設備保全を属人的なものにしがちです。例として、ベテラン社員が異動や退職をした瞬間に、現場全体の判断力が大きく低下してしまう恐れがあります。若手社員や新任者にとっても「何を基準に判断すれば良いのか分からない」「結局最後はベテランに聞かないと決められない」という状況が続けば、スキルの習得や人材育成の機会も失われてしまいます。
状態基準保全(CBM)は、本来こうした属人的な判断から脱却し、誰でも一定の基準で設備状態を把握・判断できる体制をつくるためのものです。にもかかわらず、データ活用の仕組みが整わないままではベテラン依存から抜け出せないままとなり、CBM導入の効果を十分に発揮できない状態が続いてしまいます。
このような課題を解決し、状態基準保全(CBM)の効果を最大限に引き出すには何が必要なのでしょうか?次章では、導入に欠かせない「現場データの可視化・分析」を実践するポイントやツールについてご紹介します。
状態基準保全(CBM)の導入には「現場データを可視化・分析」できる環境が不可欠
状態基準保全(CBM)を導入したが効果がない…という失敗の背景には、集めたデータを活用できる環境が整っていないことが考えられます。紙やExcelでは必要な情報をすぐに確認・分析するのが難しく、判断につながりにくくなります。
CBMを機能させるには、設備データをリアルタイムで可視化し、誰でも状況を把握・分析できる環境づくりが不可欠です。ここでは、データを可視化・分析するポイントや、実践につなげる便利なツールや保全の成功事例について解説します。
現場データを可視化・分析するポイント
CBMの導入を成功させるには、次のようなポイントを押さえることが重要です。
ポイント | 内容や例 |
---|---|
データを「見やすく、 使いやすく」整えること | 過振動・温度・圧力などのデータは一覧表示だけでなく、グラフやダッシュボードで視覚的に分かりやすく表示し、異常兆候が一目で分かるようにする |
誰でもアクセスできる 環境を整えること | 特定の担当者に頼らず、現場スタッフ全員が必要なときに情報へアクセスできる体制が必要。誰もが使いやすいシンプルな画面やフィルター機能などを整備する |
分析・判断をサポートする 仕組みを導入すること | 単なる記録ではなく、AIや統計的手法を活用した自動判定・予兆検知機能を活用し、ベテランのカンに依存しない“データに基づく判断”を実現する |
現場負担を 増やさないこと | 可視化や分析を充実させつつ、データ入力や管理作業が現場の負担とならないよう、センサーからの自動収集やレポート自動作成など省力化・効率化につながる仕組みを整える |
CBMは「データがあればうまくいく」ものではありません。現場の人が実際に使いこなせる仕組みまで整えてこそ、本当の効果を発揮します。次章では、具体的にどのようなツールやシステムがその環境づくりに役立つのか、事例を交えてご紹介します。
現場データの活用は「帳票のデジタル化」で実現!
先述したようなポイントを実現するうえで有効なツールの1つに、「デジタル帳票」が挙げられます。デジタル帳票とは、従来の紙ベースの記録をデジタル化し、PCやタブレット、スマートフォンで入力・管理できるツールです。
設備の点検結果や測定値、作業履歴などをリアルタイムで記録・共有できるため、保全業務の効率化と精度向上に役立ちます。
たとえば、「tebiki現場分析」という帳票作成ツールであれば、現場で使いやすいシンプルな入力画面と、誰でも直感的に操作できる設計が特徴です。点検結果や異常発生時の記録をその場で入力できるだけでなく、蓄積されたデータをもとに傾向分析やグラフ化も簡単に行えるため、異常の早期発見や再発防止策の検討にもつながります。
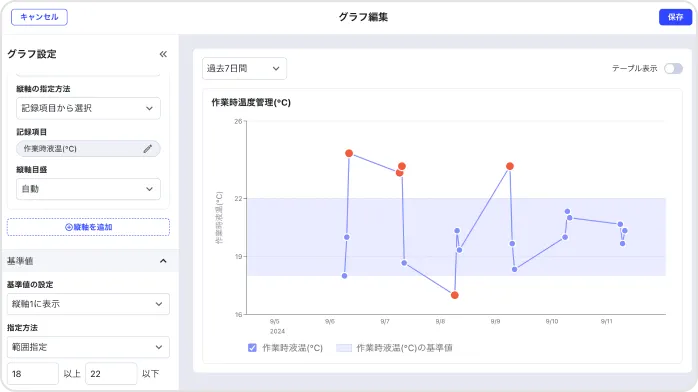
主な特徴は以下の通りです。
項目ごとに正常値設定が可能 | 正常値以外の記録は異常値として管理者にアラートが届く |
使いやすい画面設計 | デジタル端末に不慣れでもタブレットでかんたんに操作可能 |
正しい現場データを蓄積 | マスタの登録、バーコード読取による情報入力、画像記録も可能 |
データ分析の専門知識は不要 | パレート図や管理図、テーブル形式の表示が自動で更新 |
帳票の検索機能やCSV出力など、管理面の機能も取り揃えています。tebiki現場分析のより詳細な情報は、以下のリンクをクリックして概要資料をご覧ください。
>>誰でも簡単にデジタル帳票が作成!分析・異常検知もできる「tebiki現場分析」の特徴をもっとみる
デジタル帳票による保全の成功例
デジタル帳票(tebiki現場分析)を活用し、保全業務に成功した企業例を2つご紹介します。
- 株式会社日ピス福島製造所:記録のデジタル化で設備停止要因を分析し、チョコ停を削減
- 株式会社日本電気化学工業所:異常値アラートで設備トラブルを検知し、故障を未然防止
株式会社日ピス福島製造所
株式会社日ピス福島製造所は、リケンNPRのグループ企業として1982年に操業開始し、主に自動車のエンジン部品を製造しています。
課題 | tebiki現場分析の導入効果 |
---|---|
・記録を可視化するまでのスキルや時間が不足していた ・監督者が帳票を確認しにいく手間も発生していた ・紙帳票では異常の発見がしづらく、対応が遅れていた | ・設備停止要因を分析し、対策できるようになった ・記録入力と同時にデータを可視化できるため、分析の工数が削減された ・リアルタイムのデータを確認し、進捗管理ができるようになった |
同社では、”生きたデータ活用”ができていないという課題を抱えていました。例として、とある製造管理記録の数値が前月比で1.4倍になっていたにも関わらず、紙で記録していたため発見が遅れたことや、蓄積した記録をグラフ化することが現場の負担になり、進まないという状況でした。
そこで、課題解決のためにtebiki現場分析を導入。作業者がデータを記録するだけでグラフがリアルタイムに更新されるため一目で変化が見えるようになり、監督者が現場に状況を見に行く時間が大幅に短縮されました。
特に、生産実績帳票をグラフ化したことで「段取り」の停止時間に人による差があることが判明し、停止時間がかかっている作業者への標準化教育を通じて、設備稼働の効率化が可能になりました。
同社が感じるtebiki現場分析の「使い心地」や、生産性向上に向けての取り組みについて詳しく知りたい方は以下のインタビュー記事をご覧ください。
インタビュー記事:設備停止は”作業者ごとのバラつき”が要因だった。スピーディな要因分析の方法とは
株式会社日本電気化学工業所
株式会社日本電気化学工業所は、1935年の創業以来アルミニウムの表面処理を専門に行い、主にアルマイト加工を手がけています。
課題 | tebiki現場分析の導入効果 |
---|---|
・異常値の検出に時間を要し、迅速な対応が難しかった ・収集したデータを活用した改善活動につなげられていなかった ・各現場の帳票を確認して押印する作業に工数がかかっていた | ・データのリアルタイム監視ができ、異常の早期発見と迅速な対応ができるようになった ・データの蓄積と分析が容易になったことで、長期的な品質改善計画の立案も可能に ・全記録を一覧でき、異常値含めて承認作業の確認時間が大幅に短縮 |
同社では、紙ベースの帳票管理が主流で記録が目的化し、収集したデータを効果的に改善活動に活かせないという課題を抱えていました。例として、異常値の検出には時間を要し、迅速な対応が困難。膨大な紙の記録からの過去データ参照や傾向分析には相当な労力がかかり、「データ駆動型の品質管理」が実現できていませんでした。
そこで、記録のデジタル化を進めるためtebiki現場分析を導入。データの蓄積と分析が容易になり、長期的な品質改善計画の立案が可能になったと報告されています。実際に、現場帳票をデジタル化し管理図をもとに設備の温度データをリアルタイムで検知したところ、通常の温度パターンとは異なるデータに気づき、設備の配管に穴が開いていたというアクシデントを迅速に発見し、大規模な設備停止のリスクを解消できたという事例もありました。
「ISO取得企業にとって非常に有用」と語るtebiki現場分析のおすすめポイントや、活用の様子について詳しく知りたい方は以下のインタビュー記事をご覧ください。
インタビュー記事:品質不良の未然防止をリアルタイムデータで実現。異常値検知を迅速にできた理由。
状態基準保全(CBM)を取り入れて設備の故障を未然に防ごう
設備の安定稼働や保全コストの最適化を実現するために、状態基準保全(CBM)は非常に有効な保全の手法です。状態基準保全(CBM)はリアルタイムなデータ分析を活用して設備の状態を把握し、最適なタイミングでメンテナンスを行うことで、無駄な作業を削減しながら生産性を向上させます。
今後、スマートファクトリーの進化とともに、CBMの重要性はますます高まると予測されます。特に、AIの進化による故障予測の精度向上や、ロボティクスを活用した自動メンテナンスの普及により、CBMの適用範囲はさらに広がるでしょう。
一方で、最新技術の導入にはコストや時間がかかるのはつきもの。そこで、おすすめしたいのが「帳票のデジタル化」です。特におすすめなツールの「tebiki現場分析」では、誰でも簡単に現場帳票を作成可能。さらに、異常をリアルタイムで検知して品質不良を防止する機能もあり、現場管理の精度向上に役立ちます。
本記事でご紹介したtebiki現場分析の資料は、以下の画像をクリックいただくと無料でダウンロード可能です。現場帳票の電子化や現場のペーパーレス化を検討されている方は、是非ご覧ください。