かんたん動画マニュアル作成ツール「tebiki」を展開する現場改善ラボ編集部です。
ポカミスとは主に製造業で使われている用語であり、人の不注意で発生したミスのことで、大きなトラブルを引き起こす可能性もあります。
本記事では、ポカミスの意味や具体的な事例、ポカミスが発生する原因と再発を防止するための具体的な対策について解説します。作業員の安全を担保しつつ、品質不良を1%でも減らせる職場環境をつくるためのヒントとしてご活用ください。
なお、ポカミス対策の重要性や取り組みへの考え方、製造現場ですぐに実践できるポカヨケ対策事例について専門家による解説動画を用意しています。以下をクリックするとご覧いただけますので、本記事と併せてご活用ください。
>>【視聴無料】ポカミスゼロへ!ヒューマンエラーの未然予防「ポカヨケでつくる製造現場の未来」を見てみる
目次
ポカミスとは?意味や語源、代表的な例
ポカミスとは、人のうっかりミスにより発生する問題のことです。
主に製造業で使われている言葉で、人が行うミスを要因に「品質不良」「安全トラブル」「顧客からのクレーム」といった問題を引き起こす行為を指します。製造現場以外のビジネスシーンや日常場面では、ポカミスのことを同じ意味合いである「ケアレスミス」と言い換えられることが多いです。
なお、ポカミスの語源は将棋/囲碁が由来とされています。囲碁/将棋の対局中に、不注意で思いもよらない悪手を打ち形勢不利に陥ることを「ポカ」と表現し、製造現場でも人の不注意によるミスという意味合いで使われるようになりました。
前提としてポカミスをゼロにするのは難しい
前提として理解しておきたいのが、ポカミスをゼロにするのは難しいということです。後述する「製造現場でポカミスが発生する2つの大きな原因」でも紹介しますが、ポカミスは「人由来のもの」「作業環境や設備によるもの」の2つがあります。
作業環境や設備によるポカミスについては、定期的な点検や改善をすることで限りなくゼロにすることができますが、人に由来するポカミスはどれだけ仕組み化や意識を統一したとしても完全にコントロールすることは困難です。
そのため、ポカミスはゼロにするという意識ではなく、限りなくゼロに近づける意識で取り組むのが重要です。
ポカミスの具体的な事例
どのようなものがポカミスに分類されるのか、具体的な例を紹介します。なお、ポカミスは製造業で使われる頻度が高く、代表的な事例としては以下のようなものが挙げられます。
- 作業手順書を見誤り、正しい手順を間違えてしまう
- 作業指示書の数値を見誤り、誤った数値で機械を設定して生産を進めてしまう
- 目視検査の一部項目を見落とし、不良品が後工程に流出する
- 見た目が似ている部品、原材料を誤って使用してしまう
- 誤った治具や工具を使用してしまう
ポカミスは、品質不良の発生や不良品の市場流出、労働災害など従業員の安全トラブル、顧客からのクレーム発生といった重大な問題を引き起こす可能性があるため、適切な対策を講じることが重要です。
以下では、「ポカミス対策の進め方」「ポカミスを起こさない作業手順書の作成方法」などについて、専門家による解説動画を用意しております。一定の確率で発生するポカミス対策の重要性や取り組みへの考え方などを知りたい方は、以下の画像をクリックして解説動画をご覧ください。
>>【視聴無料】ポカミスゼロへ!ヒューマンエラーの未然予防「ポカヨケでつくる製造現場の未来」を見てみる
製造現場でポカミスが発生する2つの大きな原因
製造現場でポカミスが発生する原因は、大きく「ヒューマンエラー」「作業環境や設備の問題」の2つに分けられます。
ポカミスを減らしていくためには、この2つの要素に着目することが大切です。それぞれの要素が、どのようにポカミスと関係しているのか詳しく見ていきましょう。
ヒューマンエラー(人的ミス)
ヒューマンエラーは、人的ミスと表現されることもあり、「ついつい・うっかり型」と「あえて型」に2つ分けられます。あえて型は、意図的に作業手順といった現場の標準を無視することで発生するため、ポカミスの場合は「ついつい・うっかり型」のエラーが該当します。
ついつい・うっかり型のエラーは、記憶エラー/認知エラー/判断エラー/行動エラーの4種類に分類されます。ヒューマンエラーの分類と内容について、分かりやすく表したものが以下の図解です。
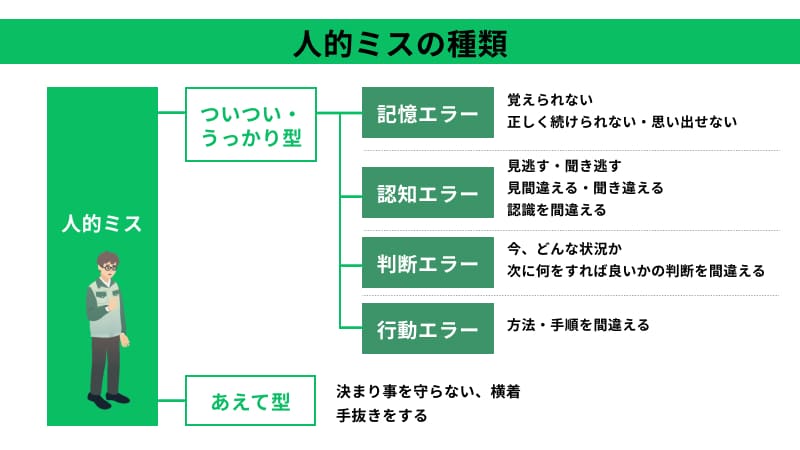
このように、ポカミスが発生する原因として、ついつい・うっかり型のヒューマンエラーによって引き起こされることが考えられます。ヒューマンエラーの対策を講じるうえで、厚生労働省は以下4つのことを意識するよう推奨しています。
- 人が間違えないように人を訓練する。
- 人が間違えにくい仕組み・やりかたにする。
- 人が間違えてもすぐ発見できるようにする。
- 人が間違えてもその影響を少なくなるようにする。
ポカミス対策に関する講演を行っていただいた高崎ものづくり研究所代表の濱田 金男氏も、講演内でヒューマンエラーの防止には「ミス発生の可能性のある手順や作業を無くしていくことが重要である」と力説しています。濱田氏によるポカミス対策の講演は、こちらから無料でご覧いただけますので、本記事と併せてご活用ください。
作業環境や設備の問題
作業環境や設備の状態によっては、ポカミスが発生する原因となります。
作業環境や設備の問題には「照度」「騒音」「温度」「5Sの乱れ」「設備不良による誤動作」などが挙げられます。作業環境や設備が原因で起こるポカミスには、以下のようなものがあります。
原因の環境 | ポカミスの内容例 |
---|---|
照度 | 光の明るさが不十分な場所で作業を行い、誤操作をした。 |
騒音 | 騒音がある場所で作業したため、聞き間違えを起こし誤操作をした。 |
温度 | 暑い場所で作業を行い、手が汗ばむことで手元が狂い作業ミスをした。 |
5Sの乱れ | 部品の分別・整理がされていないため、誤って別の部品を組み込んでしまった。 |
設備不良 | 指定された配管のバルブ操作を指示されたが、配管の敷設が複雑で別のバルブを操作した。 |
これらの防止例としては、以下の5つを意識すると良いでしょう。
- 作業エリア全体の照度を均一化させる/調光機能を備えた照明を導入する
- 遮音壁を設置する/作業内容をイメージしやすいように図示や写真を用いた手順書を作成する
- 冷暖房設備の適切な設置とメンテナンスを行う/絶縁材や遮熱材を使用する
- 定期的な5S活動を導入して作業環境を見直す
- 操作部分にラベルをつけたり、色分けを行う/スイッチに物理的なカバーをつける
特に5S活動は、現場ですぐに実践できるポカミス対策に留まらず、あらゆる現場改善に必要な取り組みの1つです。
5S活動について詳しく知りたい方は、数々の企業で5S改革を行ってきた専門家による5S活動の具体的な実践方法について解説した無料動画をご活用ください。
作業手順やルールが不明確
製造現場において、特定の作業に対する手順やルールなどが不明確な場合、作業者のスキルや経験、カンコツに依存してしまうため、ポカミスが発生しやすくなります。
作業手順が変更されているにも関わらず、周知しているルールや活用しているマニュアルが古いまま運用されているなどが考えられます。また、基準となるルールが曖昧な場合にもポカミスを誘発する原因になるでしょう。
以下の資料では、手順書があるにも関わらず手順書通りにできない理由や守らせる方法などを体系的に紹介しています。画像をクリックして、あわせてご覧ください。
【5ステップ】ポカミスをなくす対策/改善の基本的な流れ
ここからは、ポカミスが発生してから対策するまでの流れについて解説します。ポカミスをなくすためには、以下の5ステップで対策を進めると効果的です。
ポカミスの原因をなぜなぜ分析で深掘りする
まずはポカミスが起こった原因を明らかにすることが重要です。
ポカミスは具体的に起きている原因がわからなければ効果的な対策は立てられません。とりあえず思いつく対策を立てたり、根拠のない対策を立てたりしても効果は出ず、同じようなポカミスが再発してしまいます。
そのため、まずはどこに原因があるのかを明らかにしましょう。ポカミスの原因を知るために、以下の6つの切り口から洗い出すと効果的です。
- ポカミス発生時の日付・時間(特定のタイミングで発生していないか)
- 当事者へ当時の作業状況や心理状態(疲労が溜まっていたタイミングか)
- 当事者の知識や技術(スキル不足ではないか)
- 設備の問題
- 作業手順の問題
- 作業環境の問題
これらのうち、怪しい要素があれば、なぜ問題が起きたのか?どこに問題があったのか、なぜなぜ分析で洗い出すことが重要です。「なぜ起きている?」という深掘りをすることで、根本的な原因に対して対策を講じることができ、ポカミスの再発防止の効果が期待できます。
なぜなぜ分析をより詳しく知りたい方は、進め方や実践例をはじめ、実践する際のテンプレートも付属している資料も御覧ください。以下をクリックすると資料をご覧頂けます。
>>【テンプレ付き】トヨタ流「なぜなぜ分析」の実践方法とポイントを見てみる
作業員の意識/作業環境にも目を向ける
ポカミスの対策を進めていくためには、作業員や作業環境に目を向けることも重要です。
新人作業者の場合、作業手順を覚えられていない記憶エラーによるポカミスが起こりやすいでしょう。中堅~熟練作業者の場合でも、慣れを起因とする見逃しや見間違いによる認知エラーが考えられます。
ヒューマンエラーをゼロにすることはできませんが、限りなくゼロに近づけるためには「作業手順のような現場の標準を守る重要性/意識を醸成する」といったことが大切です。
また、作業環境に問題がないか目を向けることも大事です。
作業環境が「暗い」「騒音がひどい」「暑い」といった注意力を下げるような状態だと、作業員はストレスを感じてしまいポカミスに繋がります。自社の作業環境に問題はないのか、現場の作業員とコミュニケーションをとりながら見直しましょう。
設計や製造、品質管理、海外工場管理などの製造業務に45年間従事してきた濱田 金男 氏の講演によると、ポカミスの原因となる作業環境には、「騒音」「照度」「温度」「湿度」といった物理化学的環境と「作業スペース」「作業姿勢」といった人間工学的側面があると解説しています。
手順/工程のルールを見直し変更する
ポカミスの原因を特定し対応策を検討した際には、手順や工程にも変更が必要にならないか確認をしましょう。
作業手順が変わるような変更は、ポカミス同様に品質や安全のようなトラブルの原因となる4M変更に該当します。トラブルを再発させないためにも、対策に付随して手順や工程のルールなど変更点の管理が必要か確認をしましょう。
また、ヒューマンエラーを限りなくゼロにする視点として、「現状の工程に問題はないか」「そもそも現在の手順が正しいのか」など、より手順を簡略化できないかという視点で見直しすることも効果的です。
見直しを行う場合、Eliminate(排除)/Combine(結合)/Rearrange(交換)/Simplify(簡素化)の頭文字を用いた言葉「ECRSの4原則」の視点で確認すると効果的です。
上記の画像は、「カンコツが伝わる! 『現場で使われる』作業手順書のポイント」から抜粋しています。ECRSの視点を踏まえた手順書作成を詳しく知りたい方は、以下の資料をご覧ください。
>>「カンコツが伝わる! 『現場で使われる』作業手順書のポイント」を見てみる
変更点をマニュアルや作業手順書に落とし込む
ポカミス対策の内容など、作業手順や工程に変更を行ったら、実際に変更点をマニュアルや手順書に落とし込みます。
【作業員の意識/作業環境にも目を向ける】で紹介した、「作業手順のような現場の標準を守る重要性/意識を醸成する」ために、製造現場ではマニュアルや手順書を活用することが一般的です。対策などの変更内容を、新たな標準として現場に浸透させることを忘れずに行いましょう。
一方で、マニュアルや作業手順書の活用にあたっては、以下のような悩みに直面して製造現場で使ってもらえず形骸化してしまうケースは珍しくありません。
- 内容の作成や更新が追い付かず、現場の実態に則していない文書に
- 内容が膨大で理解しにくい/使いにくい
- 作業のカンコツを文字や写真で理解しにくい
マニュアルや手順書を形骸化させないためにも、現場で活用されているマニュアル・手順書の特徴を把握するのが大切です。以下の資料では、形骸化する理由や現場で使われる手順書作成のポイントなどを詳しく解説していますので、以下の画像をクリックしてご覧ください。
対策の効果検証を行う
対策を講じて一定期間経過した後に、効果が表れているか検証を行いましょう。
ポカミスで顕在化していた問題が不良率の上昇だとしたら、対策を実行後の該当工程における不良率の状況を確認するといったイメージです。仮に、不良率の変化が見受けられないとすると立案した対策が誤っていた/想定していた原因がそもそも違うといった可能性が考えられます。
対策を実行して終わりではなく、実際に効果は出ているのか?出ていなかったとしたら、改めてこれらのステップをやり直すといった形で、PDCAサイクルに基づいて継続的にカイゼン活動を行い、ポカミスの再発防止を実現を進めていきましょう。
ポカミス(ポカヨケ)の再発を防ぐ具体的な対策
ポカミスを防止するうえでは、発生した原因を突き止めて適切な対策を講じるのが大切です。ここでは、ポカミスを再発させないための対策について紹介していきます。
- リスクアセスメントを実施する
- 定期的なKY活動を実施する
- エラープルーフ・フールプルーフを踏まえた工程の設計を行う
- 3M(ムリ・ムダ・ムラ)を取り除く
- 5S活動を通じた保全活動を実施する
- 4Mの変化点・変更点を管理する
- 作業手順書やマニュアルを動画化する
リスクアセスメントを実施する
リスクアセスメントとは、現場に潜んでいる危険性や有害性を調査して、除去・低減するまでの一連の手法のことです。現場に潜んでいるリスクや対策方法を把握し、災害に発展するリスクを事前に取り除くことによって、ポカミスひいては労働災害が発生しないような現場にすることができます。
具体的には、リスクアセスメントに取り組むことで以下のような効果を期待できます。
- 潜むリスクを事業者・労働者全員で共有できる
- 職場に潜むリスクを可視化できる
- 必要な安全対策に対して優先順位をつけられる
- 残留リスクに対して「遵守事項」の理由が明確になる
- 職場全員の参加によって「危険」に対する感受性が高まる
リスクアセスメントについてさらに理解したい方は、専門家による「実施方法」や「手掛かりとなる「作業標準/作業手順書」のポイント」などを解説している動画をご覧ください。以下をクリックすると解説動画を視聴頂けます。
>>現場のキケンを見極める『リスクアセスメント術』を見てみる
定期的なKY活動を実施する
KY活動(危険予知活動)は、現場内に危険が潜んでいる作業や場所などの要素を洗い出して、事前にリスクの排除を行ってトラブルを防ぐ活動のことです。従業員の安全と健康を守るために非常に重要な活動であり、KY活動に参加することでポカミスの防止が見込めます。
また、KY活動によって従業員の安全意識向上にもつながり、安心して働ける環境の構築も実現するでしょう。結果として、生産性・従業員満足度の向上も期待できます。以下の動画では、元労基長によるKY活動の目的や未然防止のための4ラウンド法の進め方を解説しています。以下をクリックして動画をご覧ください。
>>元労基署長が解説!事故を未然防止するKY活動と4ラウンド法の在り方とは?を見てみる
フールプルーフを踏まえた工程の設計を行う
ポカミスが発生しないよう設計や仕組み化をするための、フールプルーフを踏まえた作業工程を設計することも重要です。ミスを防ぐのはもちろんですが、発生したとしても危険な状態に発展しないようにする意味合いもあるため、些細なポカミスが重要な事故や労働災害への発展を防止できます。
1つのミスが重大な事故・製品不良につながることも少なくない製造業では、未然に防止する働きかけが非常に重要です。
3M(ムリ・ムダ・ムラ)を取り除く
3Mとは、製造業における品質や生産性を阻害する要素である「無理(ムリ)」「無駄(ムダ)」「斑(ムラ)」の頭文字を取った考え方のことです。トヨタ生産計画(TPS)における重要な基本思想のひとつでもあります。
3Mが存在していると、整理整頓されていない現場での作業や標準化されていない作業が発生し、ポカミスにつながる可能性も十分に考えられます。最悪の場合には、不安全な機械操作や作業によって、労働災害につながることもあるでしょう。
3M改善に取り組む上では、製造業の経営コンサルティング企業「株式会社GEMBAコンサルティング」に属する「大原 健佑」氏の動画セミナー「3M(ムリムダムラ)の視点と改善 製造業の品質向上と生産性向上への鍵」をご視聴ください。
5S活動を通じた保全活動を実施する
5Sとは、整理/整頓/清掃/清潔/躾(しつけ)の頭文字を取った用語で、生産性や職場環境、業務などを向上させる活動のことです。単に現場をきれいにすることが目的ではなく、本質的な目的はその先にあり、製品品質や生産性の向上をはじめ、ポカミスが発生する原因を排除する意味合いも含まれています。
日常的に5Sを実施することによって、作業環境や機械や設備の異常などを早期の段階で発見でき、ポカミスの未然防止にもつながるでしょう。
4M変更のタイミングを理解して適切に管理する
ポカミスが発生しやすいケースの1つとして、4M(Man:人)(Machine:機械)(Material:材料)(Method:方法)が変更された時が挙げられます。例えば、Machine(機械)が変更された際に、操作方法を理解できていないために手順を間違えてしまったり、新人作業員が配置されたタイミングで、経験不足から些細なミスをしてしまったなどです。
そのため、4M変更が発生するタイミングを適切に理解し、作業手順の見直しや作業員への再教育を実施するのが重要です。4M変更についてより詳しく知りたい方は、以下の記事もあわせてご覧ください。
関連記事:4M変更とは?通知義務の有無や管理しやすくする方法も解説!
作業手順書やマニュアルを動画化する
現場で活用している作業手順書やマニュアルが紙の場合、文章/図解/画像のみで情報を伝えなければならず、読み手の解釈や経験年数などによって理解度にバラつきが発生する可能性があります。十分に作業内容や手順を理解できていないと、ポカミスの原因になることも。
理解度のバラつきをなくしてポカミスを防止するためにも、作業手順書やマニュアルを動画で作成するのが有効です。動画化することにより、作業手順や細かなカンコツを「動いている映像」で学べるので、テキストベースの手順書と比べて理解度が深まりやすくなります。
実際にマニュアルを動画化している株式会社神戸製鋼所では、紙の作業手順書から動画の手順書に変えたことにより、作業手順のミスを軽減し、従業員理解度の向上に貢献しています。同社の詳しい事例を読みたい方は、以下のインタビュー記事をクリックしてご覧ください。
インタビュー記事:動画を活用した現場の人材教育効率化と作業標準化
次の見出しからは、ポカミス対策に動画のマニュアルがおすすめである理由についてより詳しく解説していきます。
ポカミス対策には「動画マニュアル」がオススメ
「【5ステップ】ポカミスをなくす対策/改善の基本的な流れ」で解説したように、ポカミス対策(ポカヨケ)を進めていくためには、業務の標準化が不可欠です。製造現場で標準を伝える手段としては、マニュアルや手順書の運用が一般的でしょう。
しかし、従来のような文字/写真ベースのマニュアルや手順書では、細かい動作や作業のタイミングといった三次元的な動きのカンコツは伝えにくいです。結果的に認知エラーや記憶エラーを引き起こし、ポカミスの再発に繋がってしまいます。
カンコツのような現場の動きをわかりやすく伝える手段として、徐々に活用され始めているのが「動画マニュアル」です。ここからは、ポカミス対策に動画マニュアルが効果的なのか?事例を交えてメリットや効果をご紹介します。
ポカミス対策に動画マニュアルを活用するメリット
製造現場でのポカミス対策には動画マニュアルの活用が効果的です。
動画マニュアルは現場での作業工程の様子を動画撮影し、マニュアルに落とし込むことで、現場での三次元的な動きを可視化して伝えることができるため、作業員は正しい作業手順を理解しやすくなります。また、1つの動画を従業員間で共有して何回も視聴できるため、繰り返し学習によって習熟度の向上につながり、ポカミスを効率的に減らすことができます。
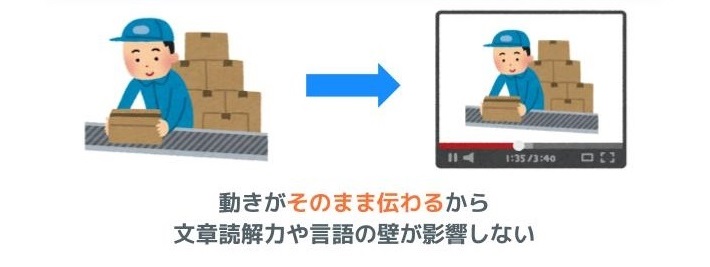
ポカミス対策として有効な手段の1つである動画マニュアルについて、より詳しく知りたい方は、メリットや紙との比較、導入ステップなどをまとめたガイドブックをご覧ください。以下のリンクをクリックするとガイドブックをダウンロードできます。
ポカミス対策に動画マニュアルを活用した事例
児玉化学工業株式会社
▼インタビュー動画:児玉化学工業株式会社▼
製品製造を行っている化学メーカー児玉化学工業株式会社では、部品を作るための膨大な作業要領書とスペイン語、ポルトガル語、中国語、ベトナム語などの多種多様な言語を話す外国人従業員が在籍しており、作業内容を正確に伝えられず、理解されないことで製品不良が発生してしまうという点に課題を抱えていました。
そこで動画マニュアルを導入し、細かい作業手順や社内ルールを正確に伝えられるようになったことで、抜本的なポカミス対策を確立することに成功しています。同社の詳しい事例を読みたい方は、こちらのインタビュー記事をご覧ください。
新日本工機株式会社
▼インタビュー動画:新日本工機株式会社▼
工作機械、遠心力鋳造管、産業機械の製造販売をしている新日本工機株式会社。同社では、作業の標準化ができていない・作業者ごとに認識が異なるなどの課題があり、品質のバラつきや作業の後戻りなど、ポカミスが発生しやすい課題を抱えていました。
そこで、標準化プロジェクトの一環としてマニュアルを紙から動画へ移行。標準化された作業を正確に若手や中堅に伝えることができ、作業品質も安定したと実感しています。同社の詳しい事例を読んでみたい方は、こちらのインタビュー記事をご覧ください。
ポカミスの対策には動画マニュアルをかんたんに作成できる「tebiki現場教育」
動画と聞くと『編集作業が難しそう…』と感じるかもしれませんが、「tebiki現場教育」であれば、製造業を中心に導入されており、動画マニュアルをかんたんに作成することができます。
tebiki現場教育には以下のように様々な機能が搭載されているのが特徴です。
- スマートフォン・タブレットで動画の撮影/編集が完結する
- 撮影した動画の音声は自動で字幕生成できる
- ワンクリックで100を超える言語に自動翻訳でき、外国人教育に活用できる
- 閲覧状況/テスト機能を活用し従業員の理解度を可視化できる
- スキルマップ機能で従業員のスキル取得状況を可視化できる
tebiki現場教育の機能や特徴などについて、より詳しく知りたい方は3分で理解できるように完結にまとめたtebiki現場教育のサービス資料をご覧ください。なお、実際の現場でどのように活用されているのか、どのような動画を作れるのかなどを知りたい方は、現場で実際に活用されている動画マニュアルをまとめたサンプル集をご覧ください。以下画像をクリックすると、サンプル集をダウンロード頂けます。
まとめ
ポカミスとは人の不注意によるミスという意味であり、製造現場におけるポカミスの代表例としては「作業手順の間違い」「安全規則の無視」「転倒による怪我」などが挙げられます。ポカミスは製品不良や事故を引き起こす可能性があるため、発生させないよう適切な対策を講じることが重要です。
また、ポカミス対策の実行には動画マニュアルがおすすめです。動画マニュアルは現場での細かい動作や作業のタイミングなどの三次元的な動きを分かりやすく伝えることができるため、作業内容への理解が深まりポカミスの削減が期待できます。
特に「tebiki現場教育」は簡単に動画マニュアルを簡単に作成できるだけでなく、100ヵ国以上の字幕翻訳機能や従業員のスキルマップ機能も備わっており、製造現場における業務標準化を効率的に実現させることが可能です。
tebikiの具体的な機能やプランを知りたい方は、以下よりサービス資料をご覧ください。